June 2019
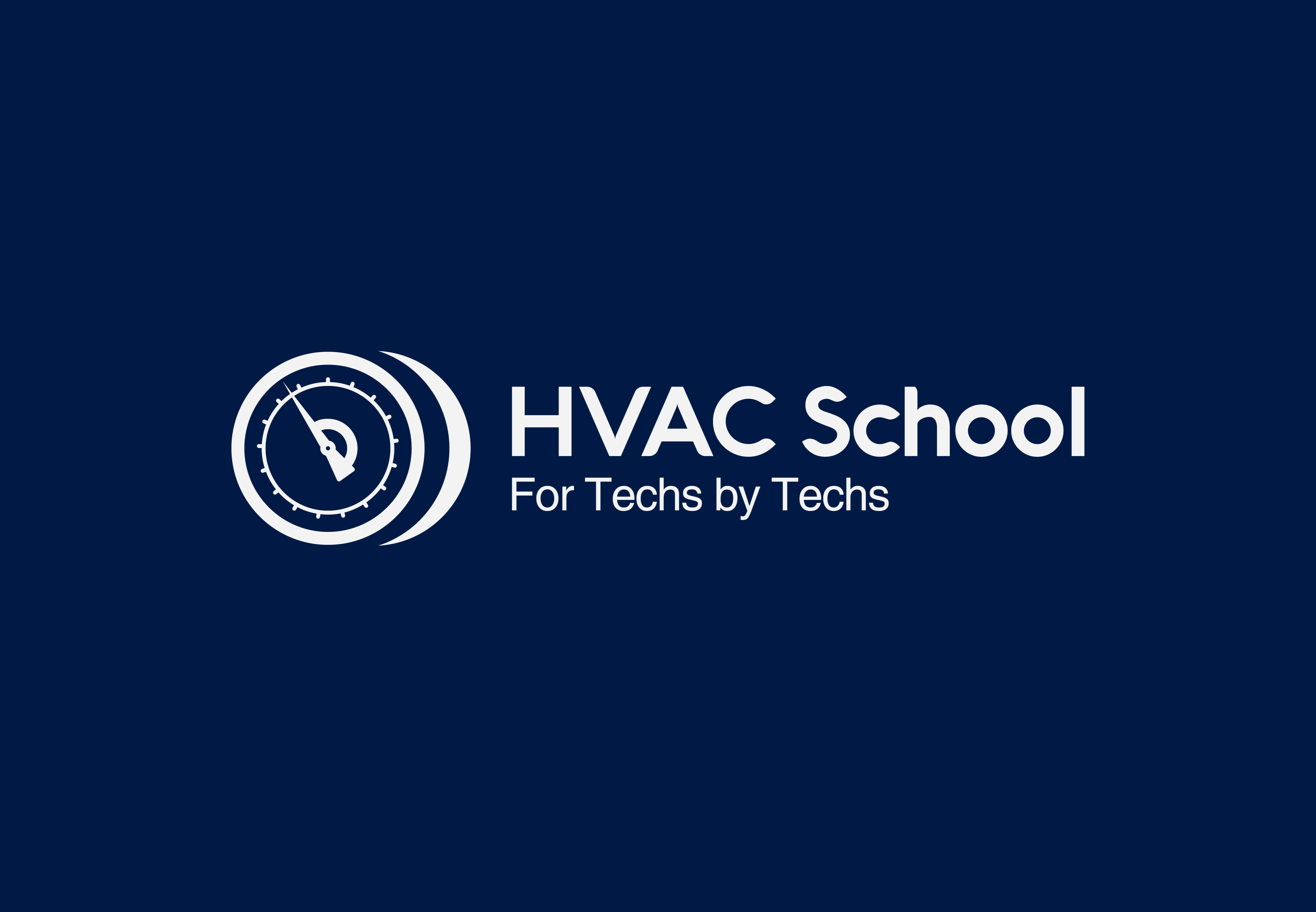
We talk with chemical and cleaning expert Ray Field on Legionnaires' disease, what it is, it’s history and what can be done to proactively prevent it.
Read more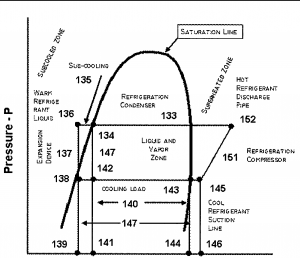
We've all heard about glide, but what is it really, and how does it affect our system? Glide, or temperature glide, is the difference between the bubble point and the dew point of the zeotropic refrigerant mixture. Well, that wasn't very helpful, was it? All we did was introduce new terms without defining them, […]
Read more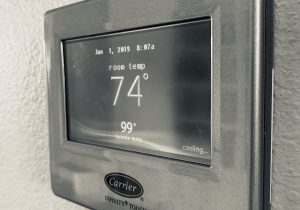
Every year when outdoor temperatures rise, there is a rash of news stories and articles about air conditioning. We had an early heatwave this year, and many people have come out and referred to the idea of a rule of thumb of what temperature you can achieve indoors based on the outdoor temperature; most commonly […]
Read more