June 2020
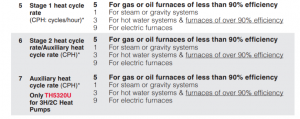
Most controls and thermostats will have some sort of cycle rate per hour setting that kicks in to prevent over-cycling once the setpoint is reached. These cycle settings don't kick in until the system starts achieving setpoint, so don't worry if it will shut off if it's set to 70° in heat mode and it's […]
Read more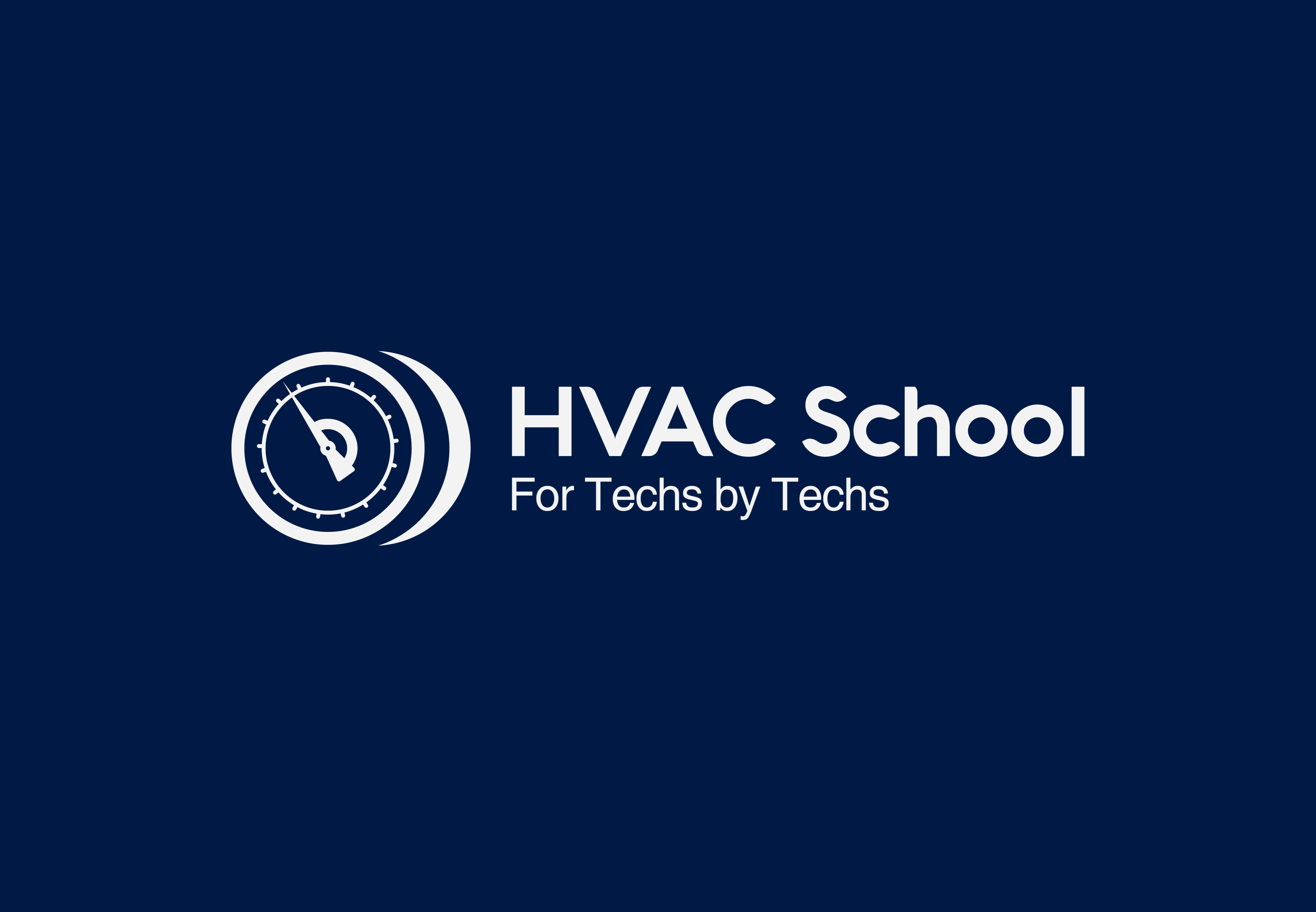
Jordan Cummings is back and we discuss some of the most important points in the proper installation of VRF / VRV systems and especially piping best practices.
Read more
When a system has abnormally high head pressure (high condensing temperature over ambient) and compression ratio, one of the easiest things to look for is a dirty condenser coil. More often than not, that will be the cause. However… There is another category of issues that can cause high condensing temperature (high head pressure), but these […]
Read more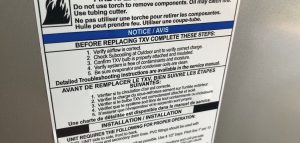
I just noticed this portion of the Carrier air handler sticker for the first time the other day. I'm like most techs; it's easy for us to ignore the great info posted right in front of us on the data tag. That's because so many of the notices contain info we are used to seeing. […]
Read more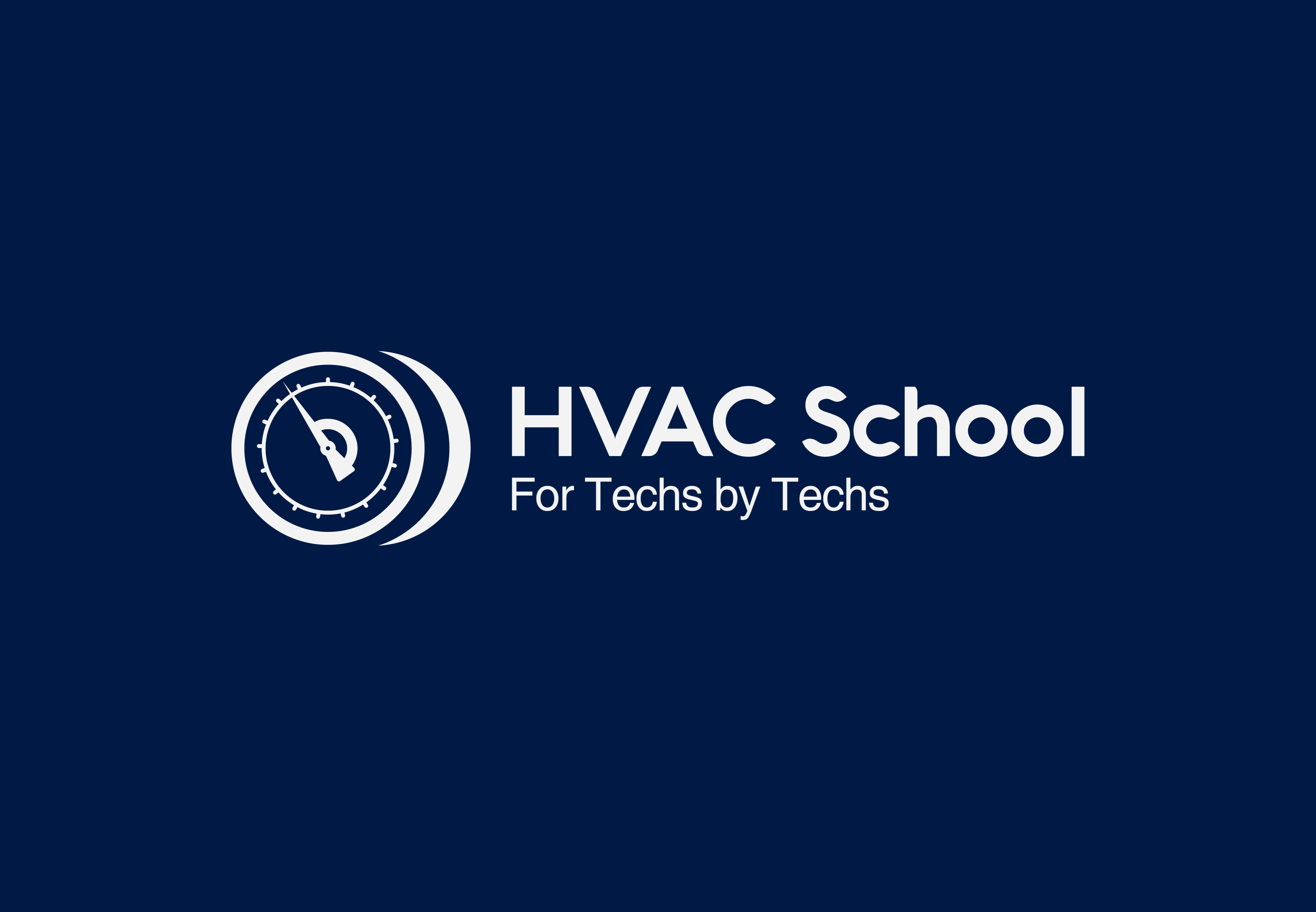
Bryan and Eric Mele have a relaxed conversation on how to manage time on the job and in life
Read more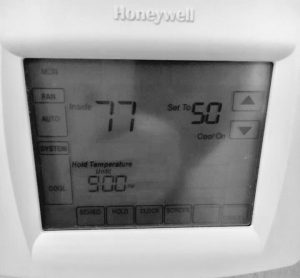
Does setting a thermostat too low cause an air conditioning system set in cool mode to freeze? The answer is no, at least not directly. However, low evaporator load (low return temperature or low airflow) and low outdoor ambient temperature can lead to evaporator coil freezing. Low indoor setpoint can lead to low return air […]
Read more