November 2020

Let's get through all of the jargon and get to the point as quickly as possible. These ratings are a calculation of how much energy you have to put into a system to get a BTU of heating or cooling out. Simple. But the problem is that each piece of cooling or heat pump equipment […]
Read more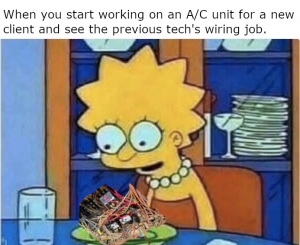
This article is based on HVAC School’s special video for 100k subscribers. The episode features Eric Mele, Andrew Greaves, and Sam Behncke as special guests. To celebrate HVAC School’s 100,000 YouTube subscribers milestone, we've released a video on a topic that applies to all sorts of HVAC techs. Customers don’t like making callbacks, and we […]
Read more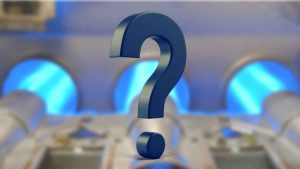
I received an email from a podcast listener with some furnace-related questions. Based on the nature of the questions, I figured it would be better to ask an experienced furnace tech. Benoît Mongeau agreed to help by answering the questions. My name is Matt and I am a newer tech (fully licensed this September, have […]
Read more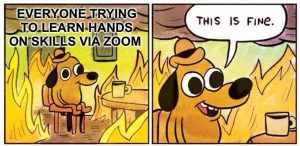
Most of the content in this article is based on Alex Meaney’s contribution to the HVAC School podcast in the October 2nd, 2020 episode: “How to Get The Most From Online Education,” which you can listen to HERE. Attending a class from your bedroom or home office sounds very convenient, right? That was probably what […]
Read more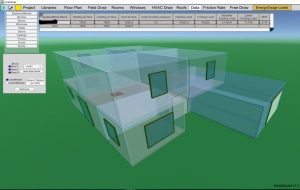
Not if you are hungry, anyways— A true story. I have a good friend who owns an HVAC company. Not much of a Ph.D., but he is known to be honest, doesn’t pull vacuums through manifolds, and claims to almost always use American-made capacitors. We’ll call him Captain Kirk. He called me recently, quite worked […]
Read more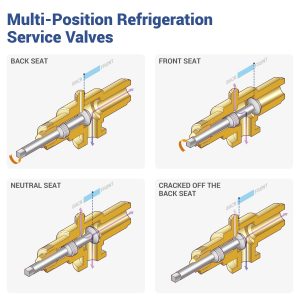
This tech tip video comes from my friend Andrew Greaves of AK HVAC and HVAC Comedy on Youtube and the HVAC Vehicle Layouts group on Facebook. Many residential techs get confused when they see these multi-position valves in larger equipment, and Andrew does a great job of demonstrating the basics in this video. In the […]
Read more