Tech Tips
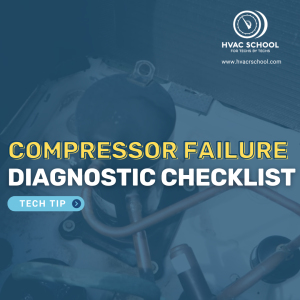
Industry data shows that up to 40% of compressors returned under warranty have no fault found. Technicians often blame the compressor when another component is the root cause. This checklist is designed to help you definitively confirm compressor failure, saving time, money, and unnecessary replacements. Let's make sure it's truly bad before we cut it […]
Read more
This tech tip was written by Eric Kaiser from TruTech Tools. Thanks, Eric! Filling refrigerant recovery cylinders is a task HVACR technicians perform regularly, but figuring out how much refrigerant to safely put into a cylinder can still be confusing. The challenge almost always comes back to refrigerant density or specific gravity. Specific gravity, also […]
Read more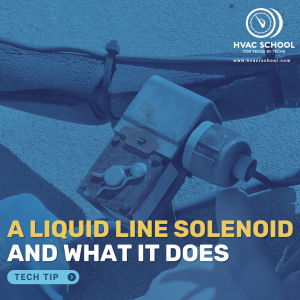
Depending on what segment of the business you are in and your location, you either work on pump-down solenoid systems all the time, or YOU HAVE NO CLUE what a liquid line solenoid is. A liquid line solenoid valve (LLSV) is just a valve that opens and closes; it has a magnetic coil. Depending on […]
Read more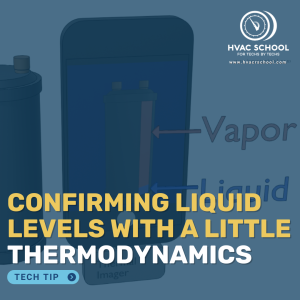
Maintaining the correct vapor-liquid refrigerant balance is crucial for air conditioning and refrigeration system performance. Longer line sets hold more refrigerant, which increases the risk of liquid accumulating in the suction line or entering the compressor during off-cycles. Heat pumps are one common application that requires additional measures. Refrigerant flow reverses during heating, turning the […]
Read more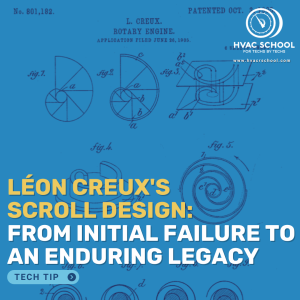
The HVAC/R industry isn’t short on tragic figures. There’s John Gorrie, whose ice machine showed a lot of promise but didn’t have enough financial backing due to the lucrative ice industry and the death of his business partner. While Gorrie may have died without seeing his vision reach the masses, he was ahead of his […]
Read more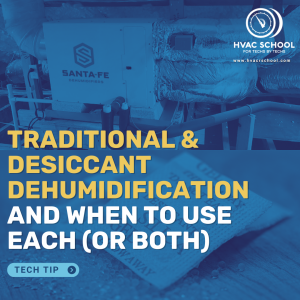
This tech tip is based on a conversation with Nikki Krueger and David Schurk. Nikki is a longtime contributor to HVAC School and is a relatively frequent podcast guest and symposium speaker. David Schurk is the Director of Applied Engineering and National Sales Manager at Innovative Air Technologies. Nikki specializes in traditional cold-coil dehumidifiers, and […]
Read more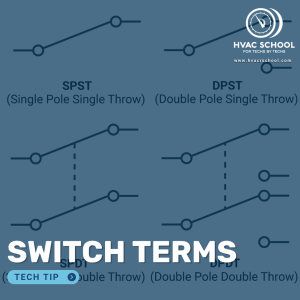
A while back, I had a tech who was having some trouble finding a 35 PSI (2.41 bar) make-on-fall pressure switch. One adjustable switch in the catalog said (SPDT), but he didn't quite understand what that meant. In that case, it means single-pole, double-throw, and the “double-throw” part means that the switch has terminals in both the […]
Read more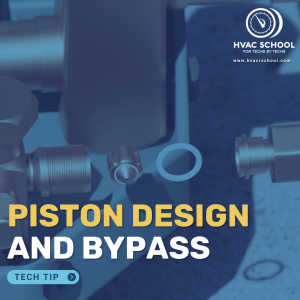
I remember it like it was yesterday. It was my first day of work as a trainee at my first technician job, just a wet-behind-the-ears kid fresh out of trade school. It was a Monday morning, and the technicians and I were standing in the dusty warehouse surrounded by stacks and stacks of brand new […]
Read more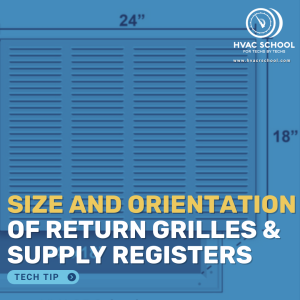
Proper sizing and orientation of grilles, registers, and diffusers may seem like such a simple thing, but it's an area where confusion and mistakes are commonly made. First, let's define some terms. Return A return draws air into a return duct system with negative pressure compared to the space, usually via a fixed “grille” (also […]
Read more