BACK
Condenser Coil Cleaning Step by Step
Coil Cleaners: A Guide to Which Cleaners to Use in Various Applications
Cleaning Condenser Coils Still Matters
Choosing HVAC Cleaners w/ Becca from Viper
Safe Chemicals are Good Chemicals w/ Mike Pastorello
#coil cleaning
Tech Tips:
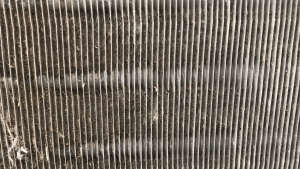
The photo above is of a real condenser coil we cleaned. The outer fins looked OK, but dirt and lint were packed deep inside. We also had sky-high head pressure and condensing temperature; those are telltale signs of an impacted condenser. That situation illustrates that a coil can sometimes look OK at first glance but […]
Read more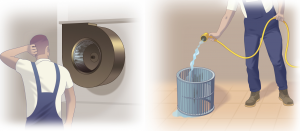
Spring and fall are the seasons where all service technicians get turned into janitors. Some techs see this as a chore and don’t particularly enjoy the routines of checklist maintenance. However, it is important to remember that the “shoulder seasons” provide an opportunity for us to perform vital maintenance on systems in order to keep […]
Read more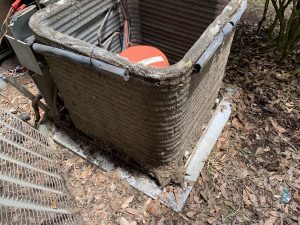
There was a story that came out recently based on an ASHRAE study performed by David Yuill from the University of Nebraska. The study appeared to indicate that condenser coil cleanliness makes no difference on system performance and efficiency. Those of us who have worked in the field know that coil cleaning matters because most […]
Read moreVideos:
Podcasts:
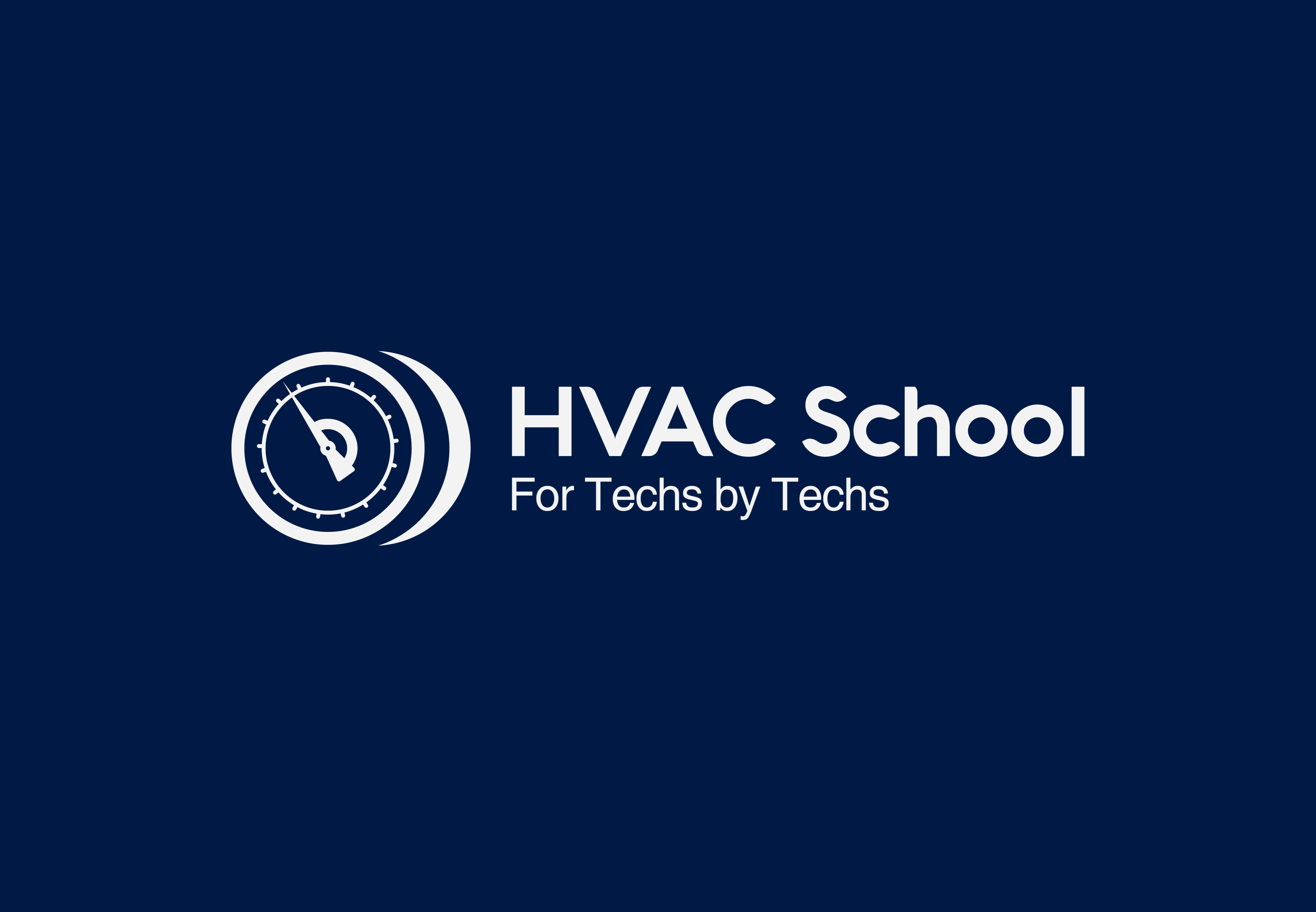
The podcast delves into the world of HVAC chemical solutions through an in-depth conversation with Becca Stamey, the marketing director at Refrigeration Technologies. The discussion provides insights into the company's unique approach to developing cleaning products, rooted in a commitment to safety, effectiveness, and customer feedback. Founded by John Pastorello, a chemist turned HVAC […]
Read more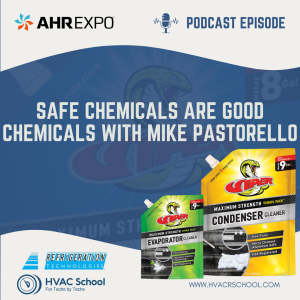
This podcast covers refrigeration technologies' growth and focus on providing safe, high-performing chemicals for HVAC technicians without hazardous ingredients. Mike Pastorello discusses the 2017 rebranding that gave their products a more modern, cohesive look. He also talks about bringing on new marketing talent like Ashley and Becca to amp up refrigeration technologies' social media […]
Read more