BACK
What is Fenestration and Why Do I Care?
AHRI Ratings Are Not Design Conditions
Observations from the Field: Insights Gained from HVAC Ride-Alongs
When Ducts Get Too Big
Size Matters — Industrial “Shortcomings”
Manual J Field Data: Ducts
Manual J Field Data: Windows
Manual J Field Data: Floors
Manual J Field Data: Walls
Manual J in 15 Minutes?
A Walk Through the Residential Design Series (ACCA Manuals J, S, and D)
ACCA Manuals in the Real World
#Manual J
Tech Tips:
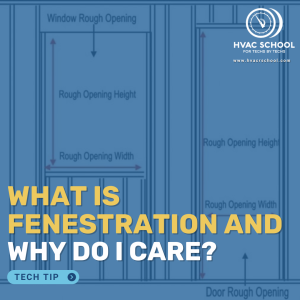
Fenestration is a fancy architectural term that means “openings in the outside of the building.” You will see this word a lot when you read ACCA Manual J or when you are doing a Manual J load calculation. Fenestration loads include heat losses and gains through windows, doors, skylights, etc., and they can make up […]
Read more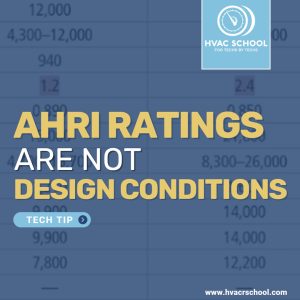
I’ve been designing a system for a home here in Dallas and noticed a couple of interesting (and disturbing!) things about the equipment’s advertised capacity vs. the actual capacity at design conditions. Equipment is rated at AHRI conditions (95 degrees outside and 80-degree dry bulb, 67-degree wet bulb inside). These conditions make equipment performance LOOK […]
Read more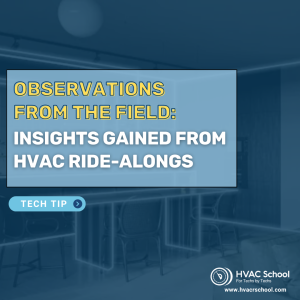
When we started Conduit, one thing that was incredibly important to us was that we constantly took lessons from the field to make sure we’re building the best product and process. HVAC Contractors around the country graciously let us ride in their trucks with them to visit customers. Our goal was to better understand the […]
Read more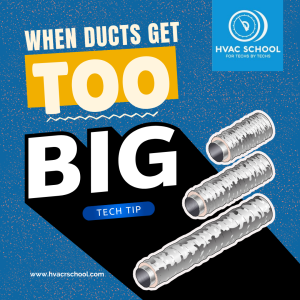
This tech tip recaps the livestream by the same name, featuring HVAC School contributors Matt Bruner and Adam Mufich, as well as special guests Russ King, Steve Rogers, and Tony Amadio. You can watch that live stream on our YouTube channel HERE. It was a beautiful day outside. The sun was shining, the birds were […]
Read more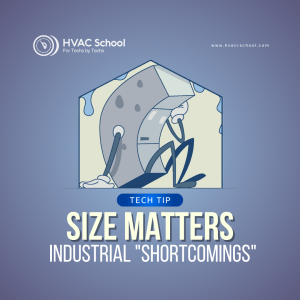
This article was written by Jennifer Manzo, an HVAC technician and the founder of HVA-Chicks Coalition. You can find her on social media as @HVAChicksjennifer. Thanks, Jennifer! It’s no secret that the HVAC industry is in the throes of an oversizing epidemic. Instead of stating the obvious, I wanted to take a deep dive into […]
Read more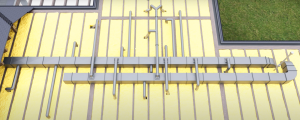
Understanding the relationships between ductwork, home comfort, and the load on a house is a complicated and dynamic problem. There are a large number of variables. Some of the data is fairly straightforward, like the other elements of field data collection we have covered so far in this series. Ductwork has different levels of insulation […]
Read more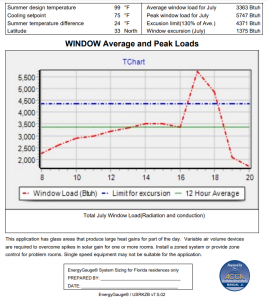
A manual J load calculation will require you to input the U-value for the windows or “fenestrations” on the house. Fenestration is a fancy construction word for window. Figuring out the U-value and SHGC of a window on an existing home is very difficult. But first, let’s dive into what the terms U-value and SHGC […]
Read more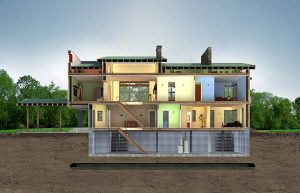
There are three types of floors: slab-on-grade, crawlspace, and basement. It should be fairly obvious when you are collecting field data as to what type of floor you are working with. Here is a brief overview of how each type affects a load calculation. Much of the information for this article comes from Allison Bailes’s […]
Read more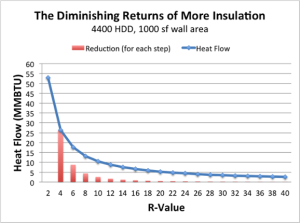
This article will cover how to collect field data for walls on an existing home for an ACCA Manual J calculation. In full disclosure, I had never collected any field data for a Manual J before I wrote this article. Many of the methods discussed were suggested by HVAC technicians and contractors in an online […]
Read moreVideos:
Podcasts:

Shelby Breger, co-founder of Conduit Tech, joins Bryan Orr on the HVAC School Podcast to discuss her company's innovative lidar-enabled design and sales software tool for HVAC contractors. Conduit Tech's software utilizes lidar sensors in iPads and iPhones to scan homes and create 3D models and 2D floor plans. It overlays load calculations factoring […]
Read moreEvents:
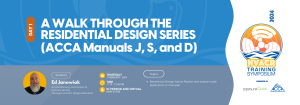
NOTE: If you cannot view the recording, the video may still be processing. The maximum wait time is 24 hours. We apologize for the delay and appreciate your patience.
Read more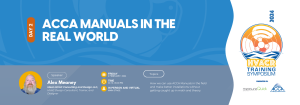
NOTE: If you cannot view the recording, the video may still be processing. The maximum wait time is 24 hours. We apologize for the delay and appreciate your patience.
Read more