August 2018
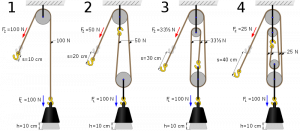
This is Part 2 series by Senior Refrigeration Tech (and prolific writer) Jeremy Smith. Pay attention to this one, folks. I know rigging and safe lifting practices may be boring to some of you, but it could very well save your back or your life. Disclaimer This article is written by a technician representing his […]
Read more
This is an open letter sent to staff at Kalos Services. Hey Everyone, First, I want to remind you that you are in no way obligated to read company emails or do anything work-related when you aren’t working. So, if you don’t want to be bothered by this on your day or time off, then […]
Read more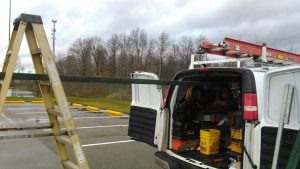
This is ANOTHER series by Senior Refrigeration Tech (and prolific writer) Jeremy Smith. Pay attention to this one, folks. I know rigging and safe lifting practices may be boring to some of you, but it could very well save your back or your life. Disclaimer This article is written by a technician representing his real-world […]
Read more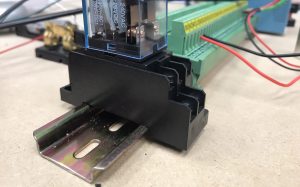
If you do any larger commercial work, you've probably seen a DIN rail without knowing what it is called. It is simply a mounting standard that originated in Germany in the 80s and slowly worked its way over here. DIN rails can be used to mount terminal blocks, relays, starters, breakers, and just about anything […]
Read more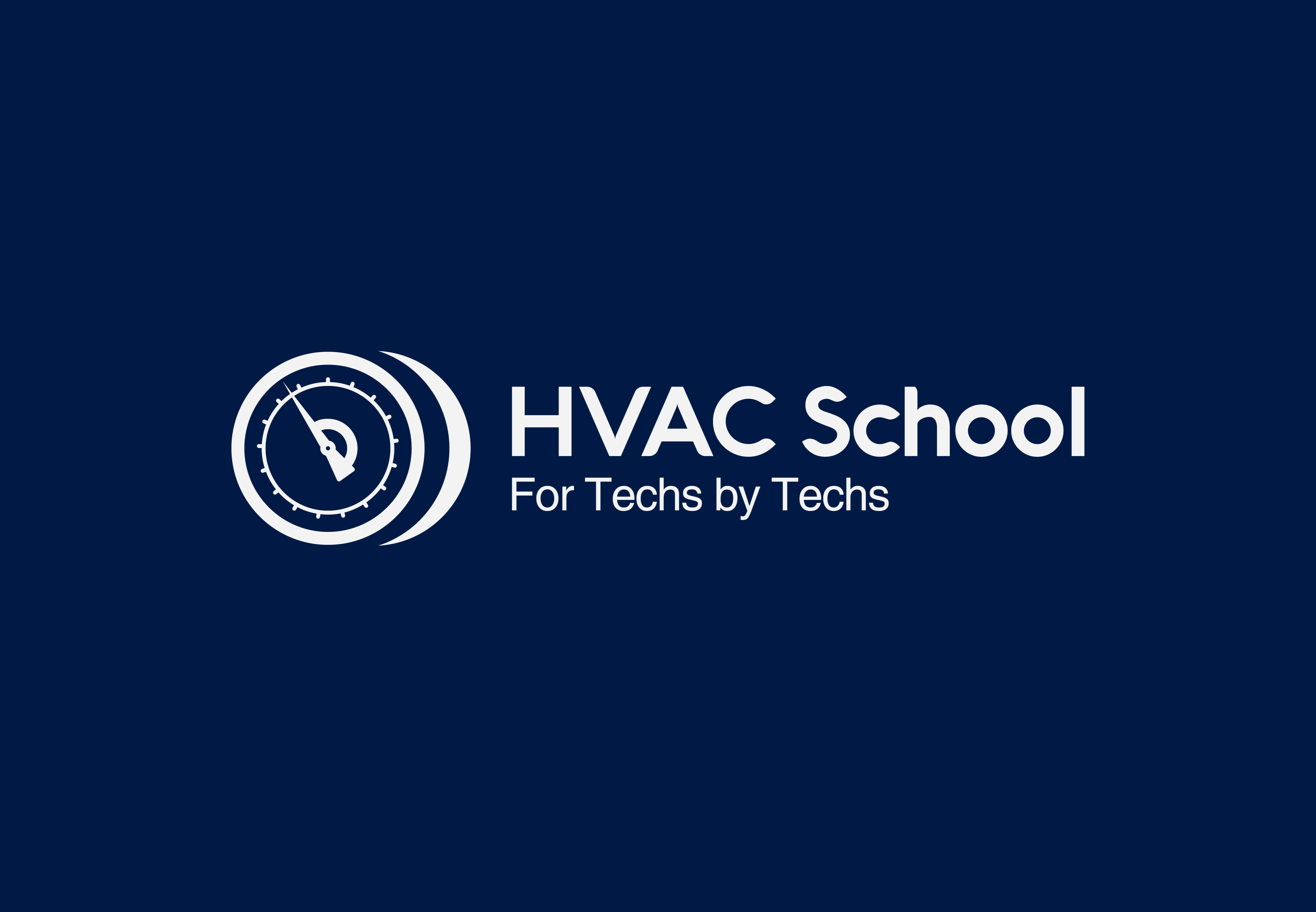
In this epsiode we talk w/ two techs recently out of tradeschool and get their perspective on their trade education and how it compares to the field
Read more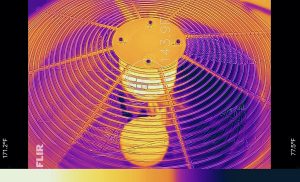
A good technician uses their senses before they use diagnostic tools. Is your suction line abnormally cold? Make sure the evaporator coil isn't frozen, and inspect for obvious airflow issues like a dirty filter or evaporator coil. Is your liquid line abnormally warm to the touch? It could be a dirty condenser, condensing fan issue, […]
Read more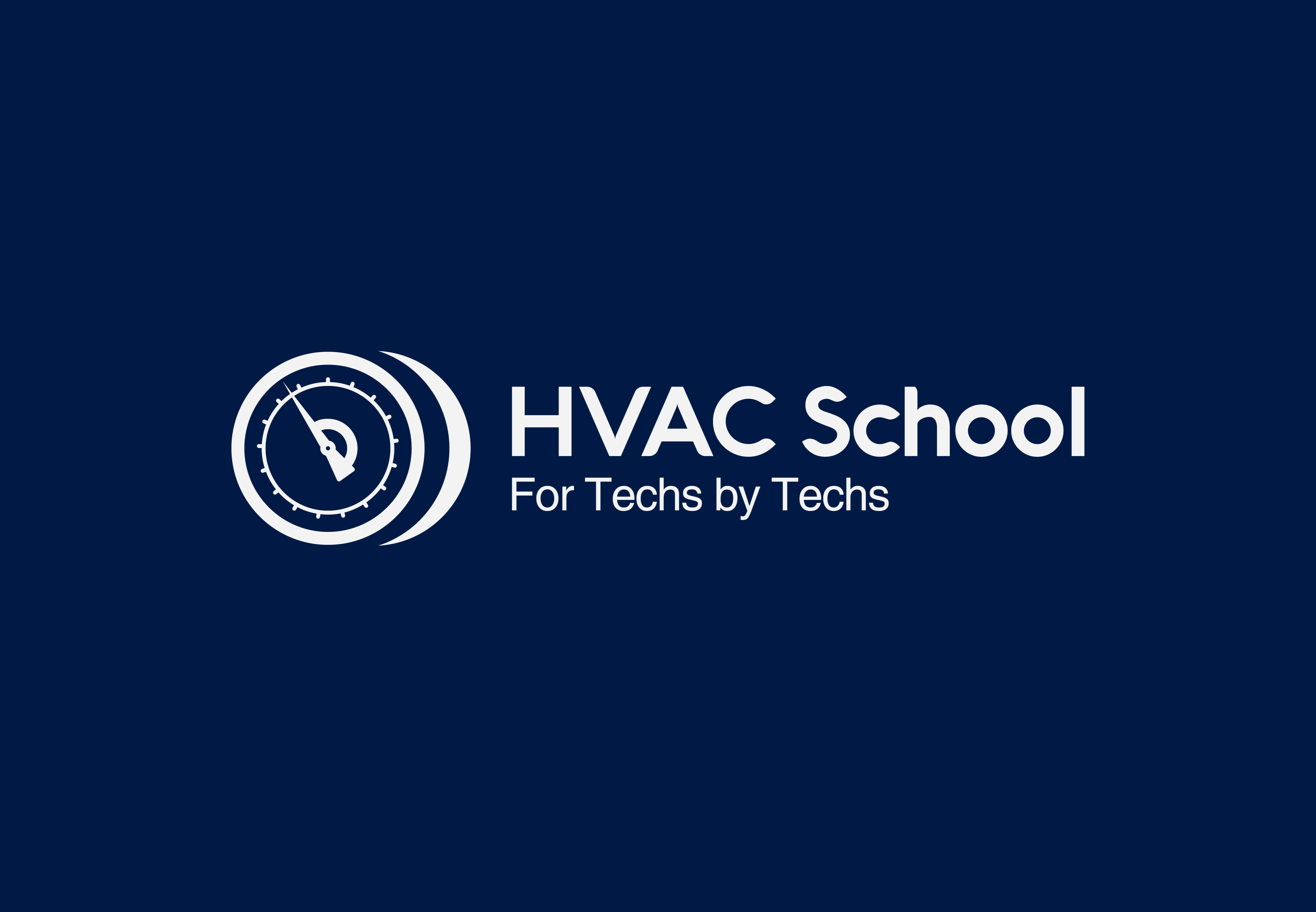
In this episode Eric dives into the world of pumps, controls, cooling towers and everything else related to the water side of a water source heating and cooling system
Read more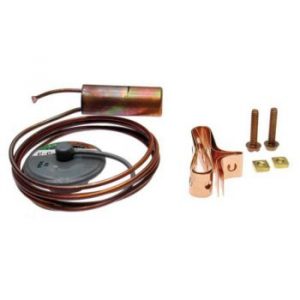
The TXV powerhead or power element is the part of the valve that sits on top of the valve to which the sensing bulb is attached. The powerhead provides the opening force for the valve by translating force from the bulb to a diaphragm in the element that forces the valve open. The sensing bulb […]
Read more