August 2019
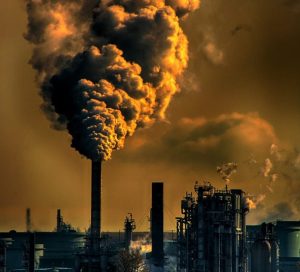
The Four Ps of IAQ I’m not the first, second, or probably even the thirty-second person to write about improving indoor air quality problems using the four Ps approach. It’s a well-known thought process in the building science community—not sure if that’s the case in HVAC circles. The first P is for pollutants. In this […]
Read more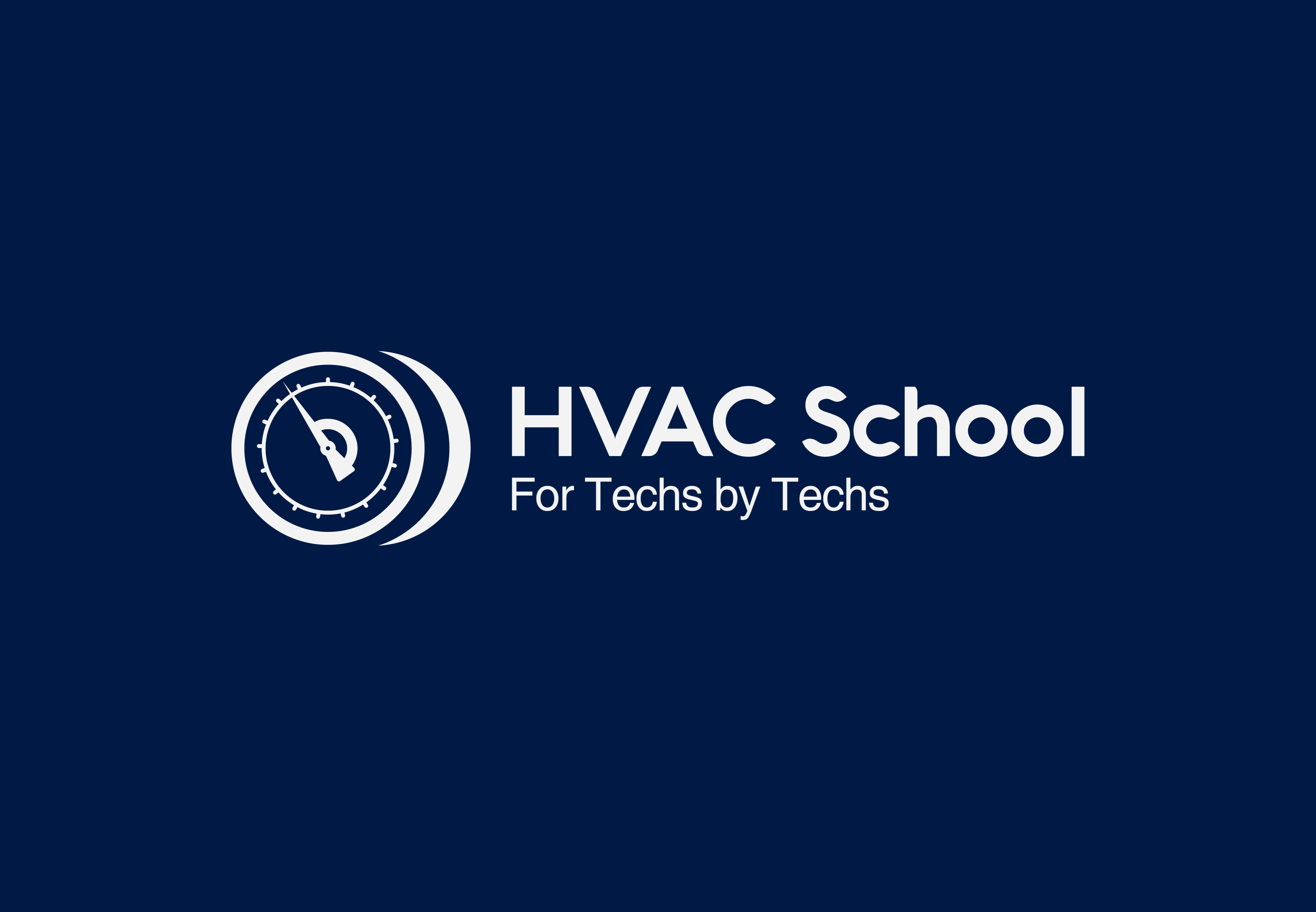
Eric joins us again and this time we are talking ECM motor types, history, diagnosis and failure prevention
Read more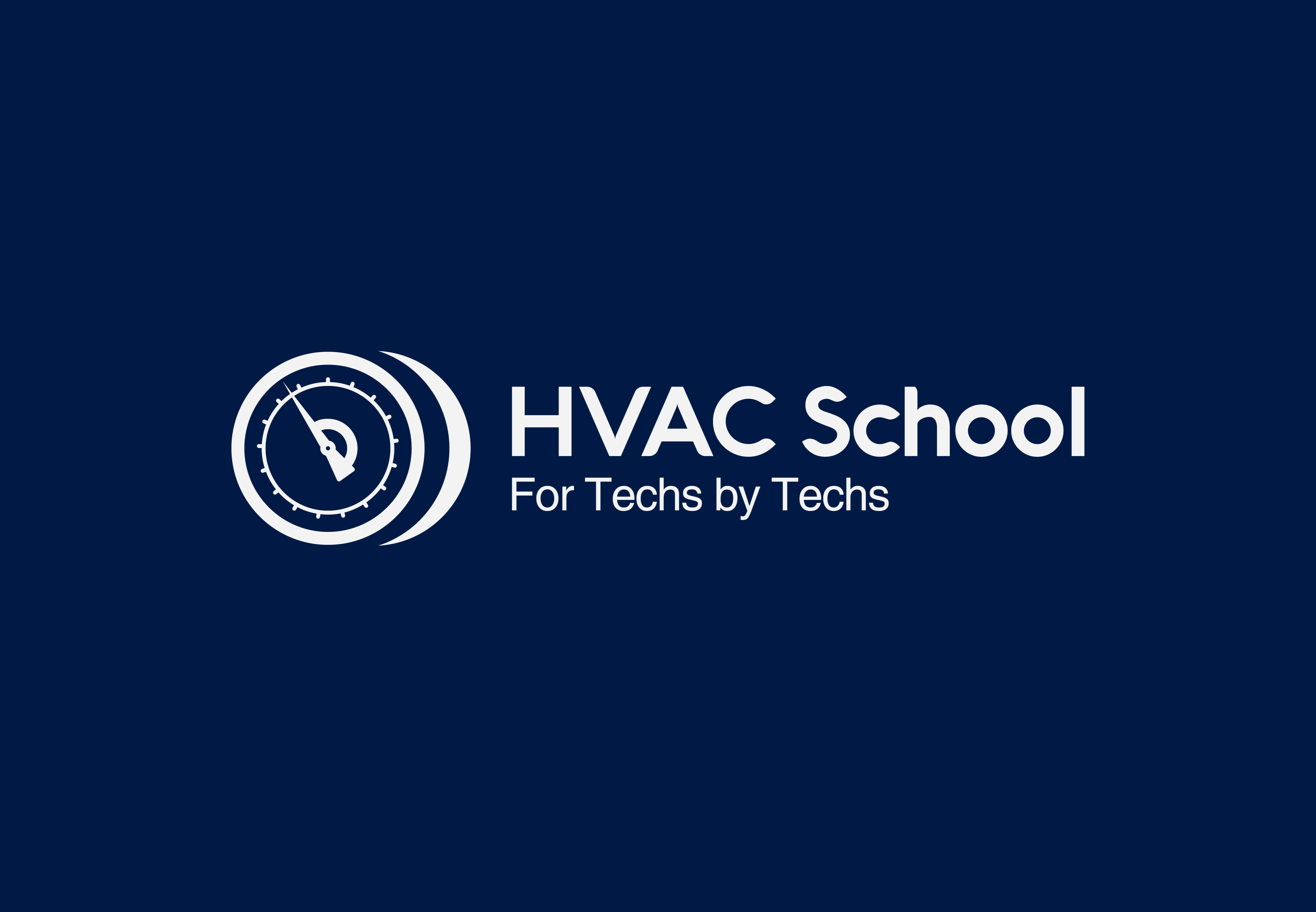
In this lively discussion we have representatives from Chemours and Bluon Energy on to talk about retrofit refrigerants and what to look for in a good retrofit
Read more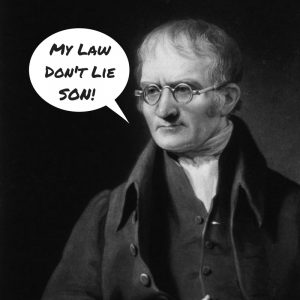
Most of the laws we refer to in air conditioning and refrigeration are pretty obvious and practical. Dalton's law of partial pressures is no exception. John Dalton observed that the air pressure was equal to the added pressures of each gas that make up air. That means that the pressure and density of air can […]
Read more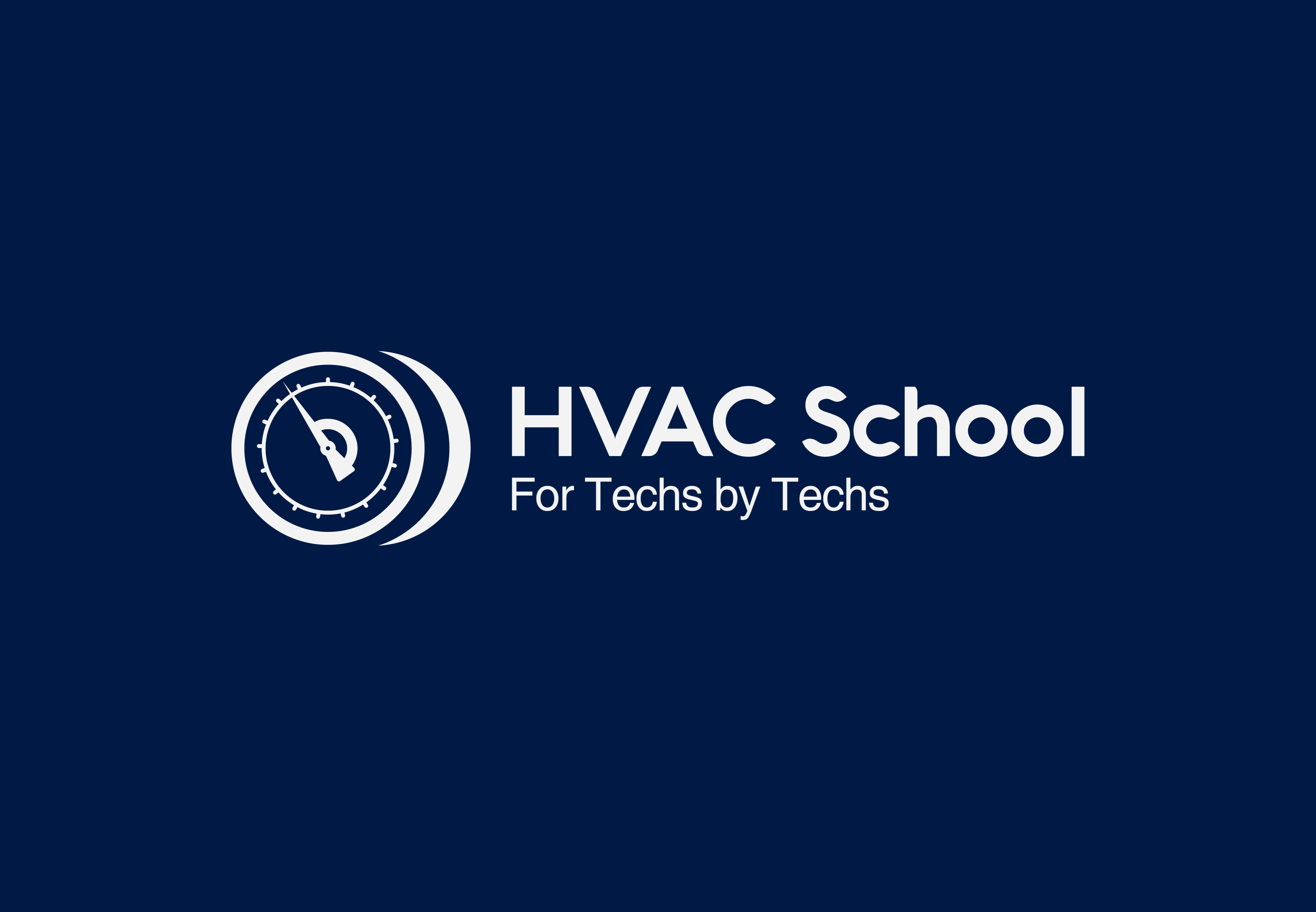
The practice and importance of trapping and vent condensate drains.
Read more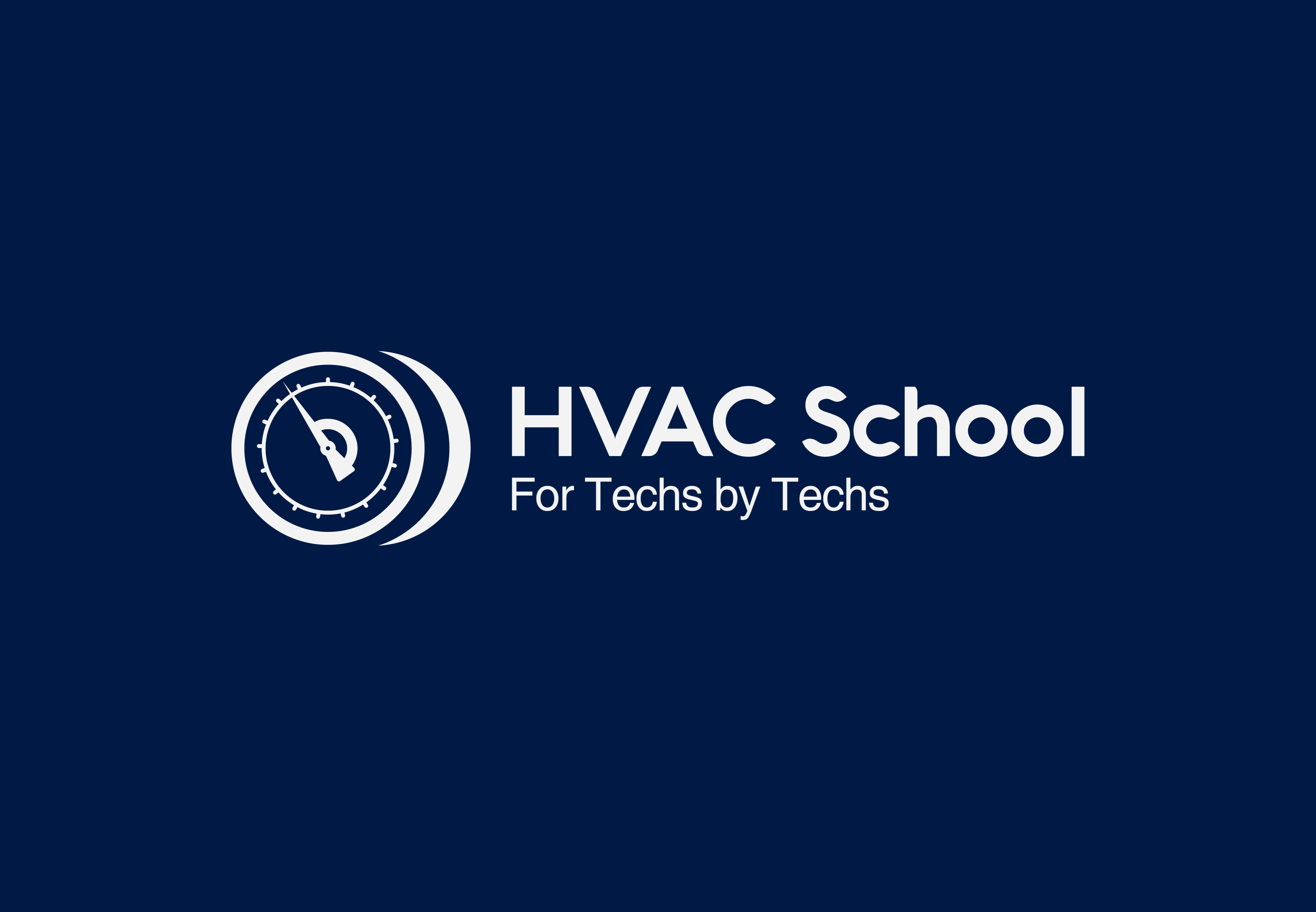
We talk through real IAQ solutions live with Jim Bergmann and others
Read more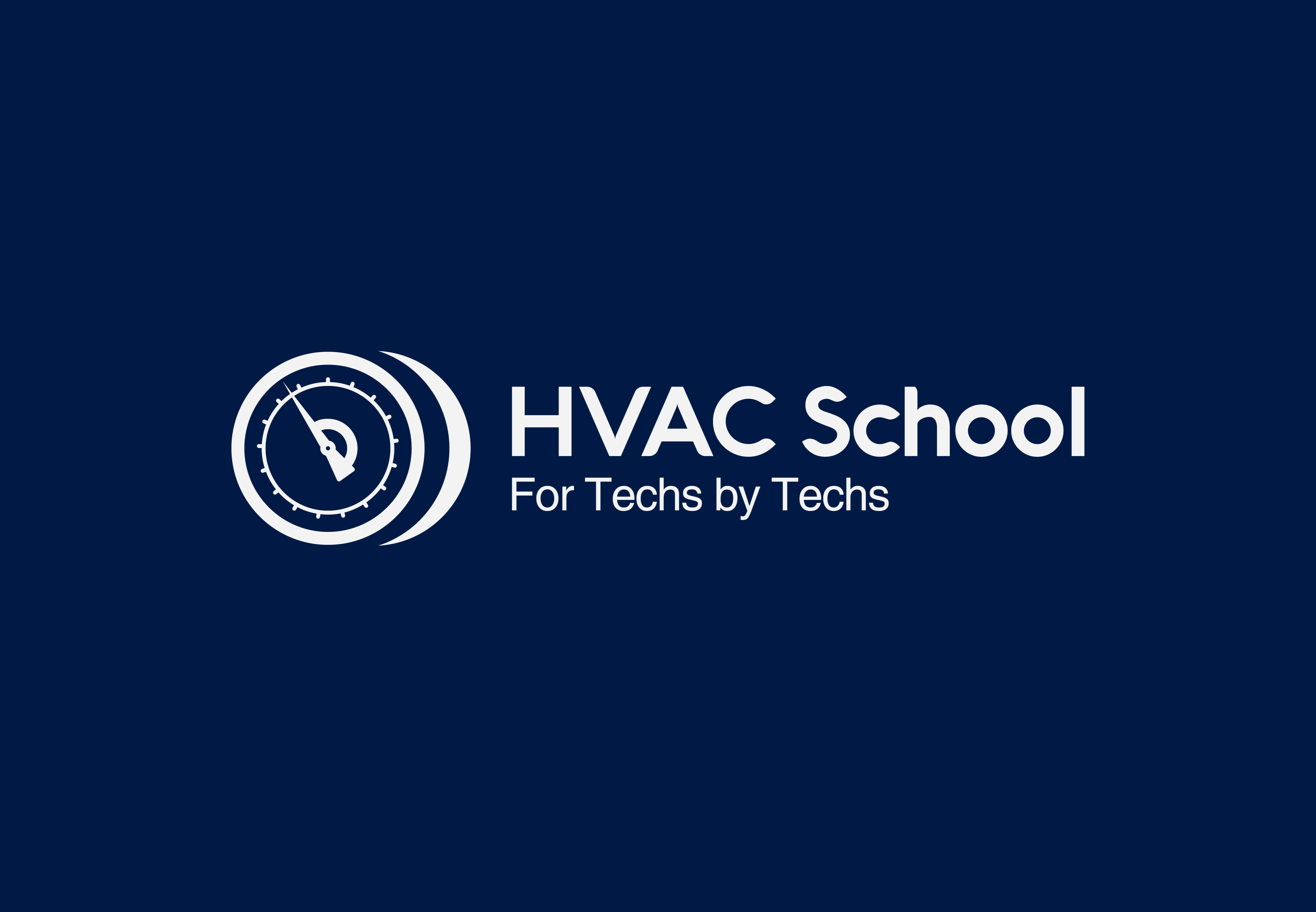
Greg of AC Service Tech on YouTube joins me on the podcast to talk refrigerant charging as well as his excellent new book
Read more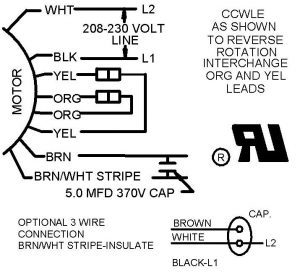
Diagram courtesy of Emerson New techs have a common question of how to wire a condensing fan motor for 3 vs. 4 wires. Jesse Grandbois submitted this tech tip to help make it simple. Thanks, Jesse! This tech tip is a quick one on the difference between wiring universal condenser fan motors and why brown […]
Read more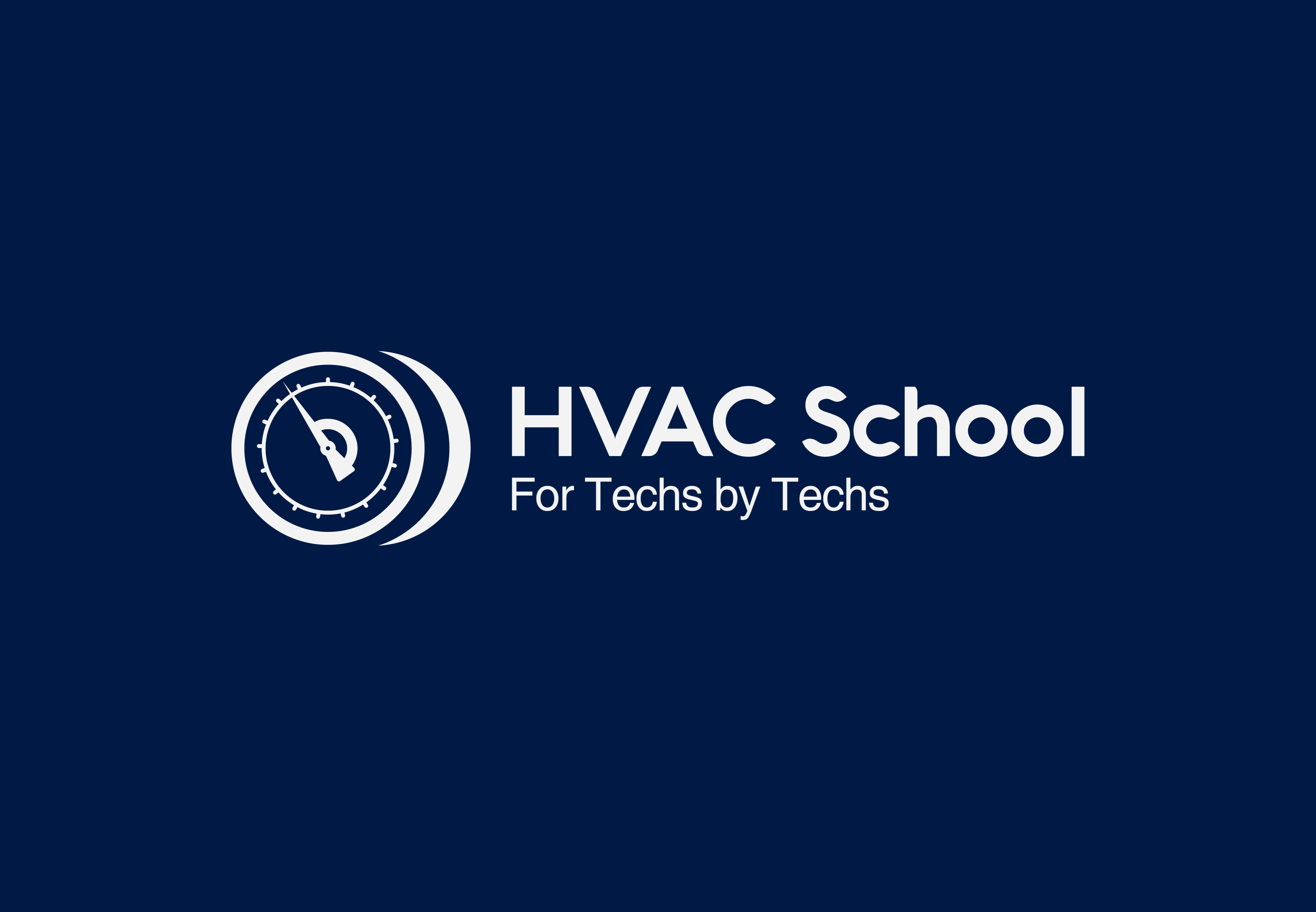
In this short and nerdy science talk I discuss how electromagnetism impacts every part of our lives
Read more