BACK
The Heating Sequence of Operations and Onions
How To Do a Heat Maintenance That Actually Matters
Practical Uses of Combustion Analysis
The Case for Buying a Combustion Analyzer
Gas Furnaces – What a Tech Needs to Know
Combustion Air
Furnace Air Temperature Rise
Combustion and Confined Spaces
Checking Evaporators on Furnaces
Q&A – Evap Placement – Short #221
All About 90% Furnaces
#furnace
Tech Tips:
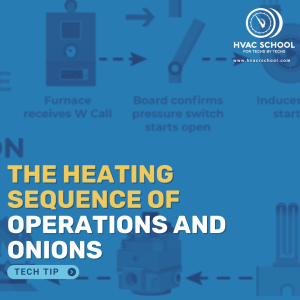
Just like Shrek, I like to think about the heating sequence of operations as an onion—it has layers. And each layer builds upon the previous one. We have written previously in great detail about gas furnaces, from top to bottom. I want to focus today on why there is a sequence of operations and how […]
Read more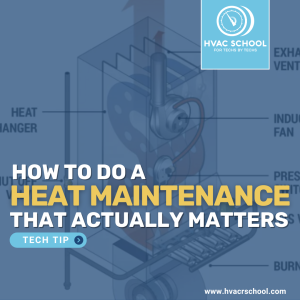
I know I’m not the only one who has sometimes felt a little bad doing heat maintenance. I remember many a day when my lead technician and I (as an apprentice) would crawl into an attic, clean the flame sensor, and then play FarmVille on our phones for 15 minutes before crawling down, giving the […]
Read more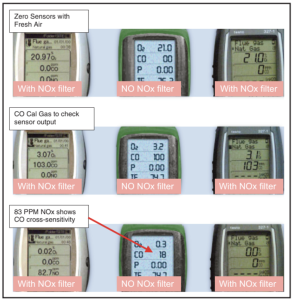
This tech tip reviews the live stream by the same name aired on November 1st, 2023. You can watch the full live stream HERE. We want to give special thanks to the guests: Jim Bergmann, Jim Davis, Tony Gonzalez, Louise Kellar, Bill Spohn, and Tyler Nelson! Gas furnaces (or any combustion equipment) create a controlled […]
Read more
Last year, I bought my first combustion analyzer. I had just started my own company and felt the additional weight of responsibility to sit down and determine the best way to verify that the furnaces I was servicing were working safely. In the past, the most extensive testing I had done was a visual inspection […]
Read more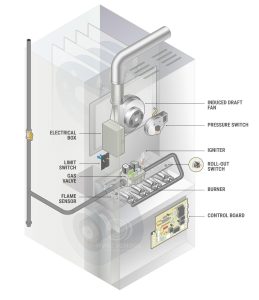
It’s that time of year again—the furnace service calls are peaking. It’s a good idea to crack open Jason Obrzut’s book, Gas Heating: Furnaces, Boilers, Controls, Components, and listen to the many public podcasts and presentations by experts like Jim Bergmann. At HVAC School, we’re fortunate to have had some of the industry’s greatest minds […]
Read more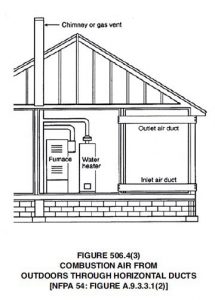
To maintain combustion (burning), you need three things: fuel, heat, and oxygen. If you have all three in the proper proportion, you can maintain a continuous state of combustion. Remove one (or reduce one sufficiently), and the triangle of combustion can collapse. In a common natural gas (NG) furnace, the heat is the igniter, the […]
Read more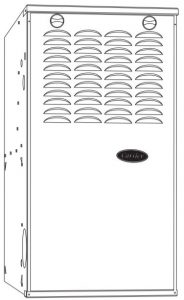
Every gas furnace data plate/tag has a specification for the temperature rise through that furnace. It is shown in a range like 50-80° or 45-75°. Those first two numbers are the lowest recommended temperature rise; the highest allowed temperature rise through the furnace is usually a 30° difference. When possible, we want to get the rise […]
Read more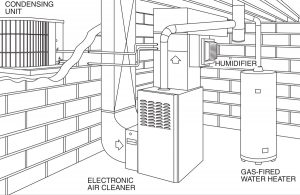
All fuel-burning appliances require oxygen to burn. They require sufficient oxygen to burn clean and safely, without soot and CO (carbon monoxide). I live and work in Florida, where most of our fuel-burning appliances are 80% efficient with open combustion. (You can learn more about the basics of combustion on a podcast with Benoit Mongeau.) […]
Read more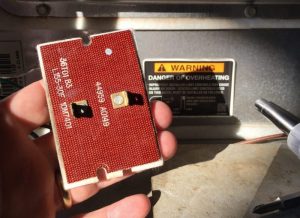
In Florida, there are not many gas furnaces—at least not as many as up north. Sometimes, we can look like real dummies compared to techs who work on them every day. One thing to know about 80% gas furnaces with cased evaporator coils is that you can often check the evaporator coil by removing the […]
Read moreVideos:
Podcasts:
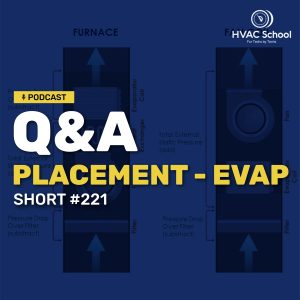
In this short podcast, Bryan talks about evaporator coil placement based on a question submitted by a listener, John. Evap coil placement differs in furnace applications versus air handlers. When we use air conditioners with furnaces, we usually put evaporator coils on the positive side to protect the heat exchanger from rusting out during […]
Read more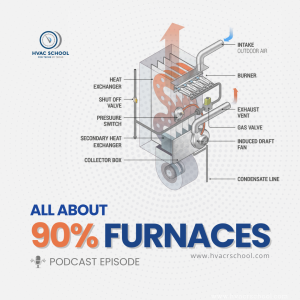
Bryan Orr hosted a live podcast discussion all about 90% efficient furnaces with HVAC professionals Ty Branaman, Adam Mufich, and Matthew Bruner. They covered the basics of how 90% furnaces work compared to traditional 80% furnaces, troubleshooting tips, and best practices for installation and service. A key difference with 90% furnaces is the addition […]
Read more