BACK
Electronic Expansion Valve Troubleshooting
Ramping Your Team Up for CO2
Setting and Adjusting Superheat on a TXV System
Flash Gas
Don’t Forget the Service Wrench
Why (and When) Do We Need Defrost?
TD of Refrigeration Evaporators
Refrigeration Pump-down Cycle
Refrigeration Gas Defrost
Are you using AI to Troubleshoot w/ Refrigeration Mentor
Pumping vs. Compression – Short #218
Building Tech Confidence w/ Refrigeration Mentor
How Do You Ramp Up Your Team to Effectively Service and Support CO2 Applications?
Residential & Rack Startup and Commissioning (Part 2)
Q&A – EPR and Pressure Limiting Valves w/ Matthew Taylor
Using Refrigerant Troubleshooting Charts w/ Joey Henderson
Rack Refrigeration Class – Part 1
How to Save Energy with Grocery Store Refrigeration
Refrigeration Mindset
The Fundamentals of CO2 Refrigeration
Introduction to Market Refrigeration for HVAC Techs
#refrigeration
Tech Tips:
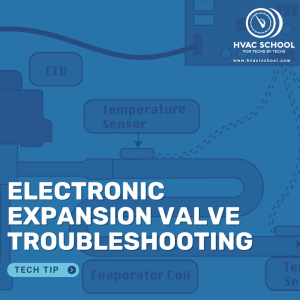
Electronic expansion valves (or EEVs) are metering devices that you’ll find in a variety of modern HVAC equipment, including heat pumps, VRF units, inverter mini splits, and chillers. This valve is electronic rather than mechanical and can precisely control the flow of refrigerant into the evaporator and optimize efficiency for heating and cooling units. Other […]
Read more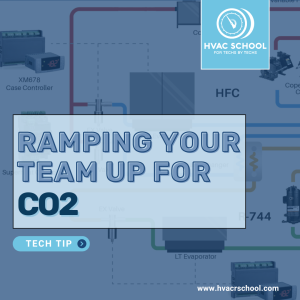
This tech tip is based on a podcast with Andre Patenaude from Copeland. You can listen to that podcast episode HERE, and we encourage you to check out some of the resources at the end of this tech tip—whether you’re all in on ramping your team up for CO2 or just CO2-curious. Carbon dioxide (CO2) […]
Read more
This is a quick tip from the “Expansion Valves – What Does and Doesn't Matter?” livestream on our YouTube channel featuring Joe Shearer, Matthew Taylor, and Corey Cruz. As metering devices, TXVs can adjust the size of their orifice to maintain a constant superheat. Some TXVs are set to maintain a specific superheat from the […]
Read more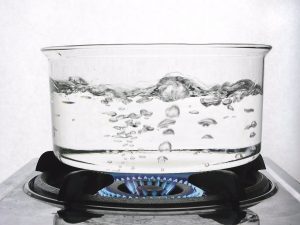
When we say that there is “flash gas” at a particular point in the system, it can either be a bad thing or a good thing, depending on where it is occurring. Flash gas is just another term for boiling. It is perfectly normal (and required) that refrigerant “flashes” or begins boiling directly after the […]
Read more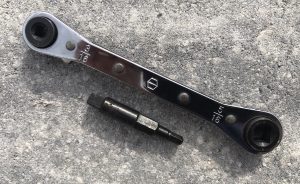
One of my most popular YouTube videos goes over how to adjust TXV superheat. It's a very simple little video that I did at my desk, and the other day I got this comment: “Good Video but I hate to say this BUT, with the title SCHOOL, why would you show the public an instructional […]
Read more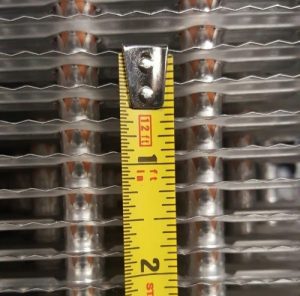
Why Defrost? Let's start with the basics and move on from there. Defrost is necessary when the coil temperature drops below 32°F. Defrost can be as simple as turning the compressor off for a period of time or as elaborate as reversing the flow of refrigerant for the whole system or just parts of the […]
Read more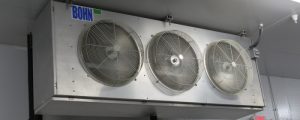
We have discussed DTD (design temperature difference) quite a bit for air conditioning applications, but what about refrigeration? Let's start by defining our terms again. Suction Saturation Temperature The saturation temperature is the temperature at which the refrigerant will be at a given pressure if it is currently changing state. This change of state would […]
Read more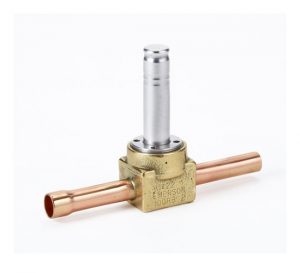
This article was written by Jeremy Smith CM, an experienced refrigeration tech and all-around great dude. Thanks, Jeremy. A very common means of control seen on refrigeration equipment is the pump down control. Why do we use this rather than just cycling the compressor off and on like a residential HVAC unit? Since most refrigeration equipment […]
Read more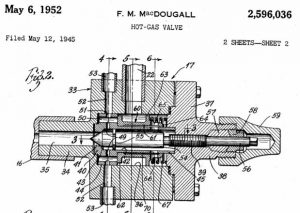
Let's take a deeper dive into the magic that is gas defrost. Most techs who are familiar with heat pumps understand the basics of a gas defrost. When we apply this strategy to a larger system where we're only reversing a small part of the system, we need to add some controls and valves to […]
Read moreVideos:
Podcasts:
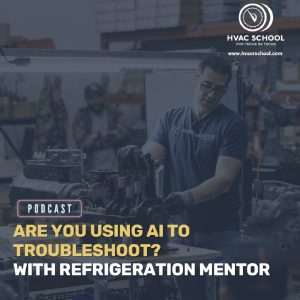
In this episode of the HVAC School Podcast, Trevor Matthews and Bryan dive deep into the transformative potential of artificial intelligence (AI) in the refrigeration and HVAC industries. They explore how AI is not a new concept in their field, discussing how manufacturers like Copeland, Sporlan, and Danfoss have long incorporated AI-driven tools and […]
Read more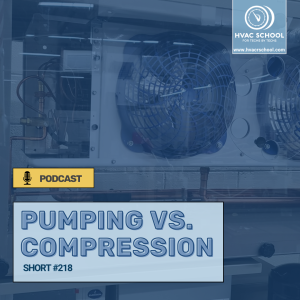
In this short episode, Bryan clears up the confusion behind pumping vs. compression. Pumping is usually associated with liquid. Liquid, like vapor, is a fluid, but it's a lot denser and is essentially incompressible because the molecules are close together. Liquid volume varies based on temperature and density, but we can't squish the molecules […]
Read more
Trevor Matthews returns to the HVAC School Podcast to discuss building tech confidence and personal growth in the HVAC and refrigeration industry. The conversation explores the transformative power of self-investment, continuous learning, and maintaining a positive mindset. Trevor shares his personal journey from a hesitant technician to a successful business owner, highlighting the importance […]
Read more
In this informative episode, Bryan Orr speaks with Andre Patenaude from Copeland about CO2 refrigeration systems. They dive deep into the unique characteristics and challenges of working with CO2 as a refrigerant, providing valuable insights for HVAC and refrigeration professionals looking to expand their knowledge in this growing field. Andre explains the reasons behind […]
Read more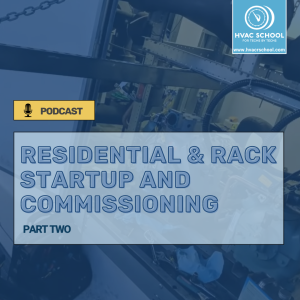
In this episode, Bryan and Max discuss commercial supermarket startup and commissioning with comparisons to residential HVAC work. Max, who has transitioned from residential air conditioning to supermarket refrigeration, shares his insights on the unique challenges and requirements of this specialized field. The conversation begins by emphasizing the critical importance of safety in supermarket […]
Read more
In this episode, Matthew Taylor joins the podcast to dive deep into the world of pressure-limiting valves and regulators used in refrigeration and air conditioning systems. They explore the intricacies of Maximum Operating Pressure (MOP) expansion valves, Evaporator Pressure Regulators (EPR), and Crankcase Pressure Regulators (CPR), discussing their functions, applications, and differences. The conversation […]
Read more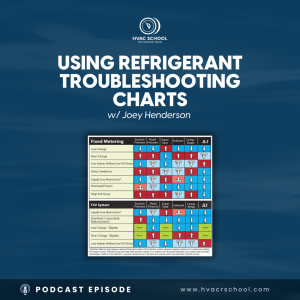
This episode focuses on understanding and effectively utilizing various refrigeration system charts and measurements for troubleshooting and diagnostics. Joey Henderson, an HVAC veteran and trainer, shares his wealth of knowledge and experience on this topic. Joey starts by discussing the challenges he faced early in his career when trying to make sense of the […]
Read more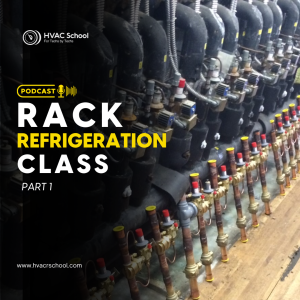
This podcast episode is Part 1 of a Kalos class on rack refrigeration given by Matthew Taylor. This first segment focuses on the basic refrigerant circuit and oil management of a parallel rack system, common in market refrigeration. Parallel racks follow the same general process as any other compression refrigeration system. However, they contain multiple […]
Read more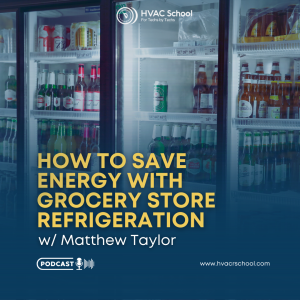
This podcast episode focuses on practical ways to save energy with grocery store refrigeration systems, with Matthew Taylor from Kalos Services sharing insights from both a technician and business owner perspective. The hosts emphasize that proper, consistent operation and preventing short cycling of compressors can have a major impact as the largest power consumers. […]
Read moreEvents:
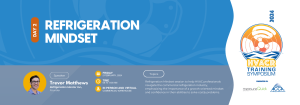
NOTE: If you cannot view the recording, the video may still be processing. The maximum wait time is 24 hours. We apologize for the delay and appreciate your patience.
Read more
NOTE: If you cannot view the recording, the video may still be processing. The maximum wait time is 24 hours. We apologize for the delay and appreciate your patience.
Read more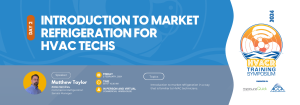
NOTE: If you cannot view the recording, the video may still be processing. The maximum wait time is 24 hours. We apologize for the delay and appreciate your patience.
Read more