BACK
CO2 Booster Systems (Codenamed CO2 is Interesting and Weird)
Solenoid Facts
Commercial Refrigeration Compressor Operation
Basic Refrigeration Startup & Commissioning
Refrigeration Equipment Diagnosis Method
Reach-In Temperature Controls
EPR valves 101
Solving & Preventing Oil Issues in Rack Refrigeration
Tips for Supermarket Rack Service w/ Trevor
Wiring Refrigerated Cases w/ Nathan & Phil
Commercial Refrigeration for A/C Techs w/ Dick Wirz (Podcast)
Refrigeration Tips For A/C Techs
#refrigeration
Tech Tips:
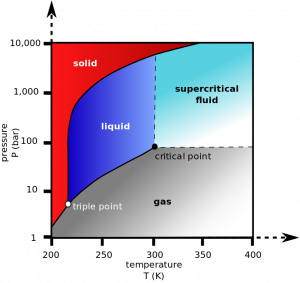
Illustration Courtesy of Emerson CO2 is a pretty nice refrigerant. It has zero ODP (ozone depletion potential) and a GWP (global warming potential) of 1. CO2 has been used as a refrigerant almost from the very beginning of refrigerants, and it's been making a big comeback in market refrigeration (especially in colder climates). CO2 […]
Read more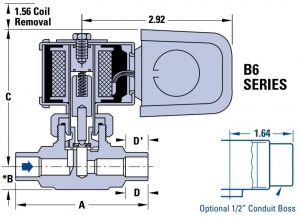
Do you know how a solenoid valve works? Really? On the surface, I think we all understand how a solenoid valve works. The coil energizes, creating an electromagnet. That temporary magnetism lifts an iron plunger within the valve allowing refrigerant to flow. But is it really that simple? It turns out that the answer isn't […]
Read more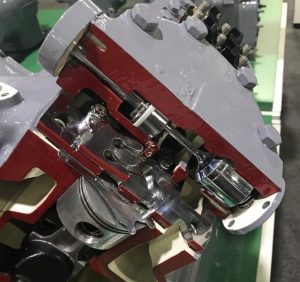
Basic Compressor Functions The compressor's job is to circulate refrigerant through the system by means of vapor compression, similar to the way your heart moves blood through your circulatory system. Refrigerant circulation is measured in lbs/min or lbs/hour; this is called mass flow rate—the mass flow rate changes depending on the density of the refrigerant […]
Read more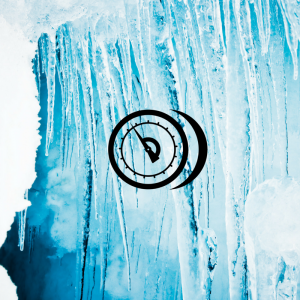
Let's take a walk through the startup and commissioning procedure of a conventional or “single” refrigeration condensing unit. We’re going to start with a unit that is fully piped in and has been pressurized for leak and strength testing. For brevity, we are going to assume a basic familiarity with industry standards, company and customer […]
Read more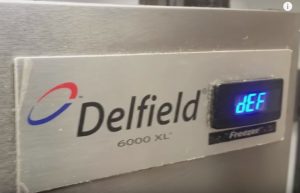
I was watching this video on the HVACR Videos channel by my friend Chris Stephens, and I was impressed by how completely he diagnoses the system both visually and with his tools. Take a look. I say this all the time, but a good, efficient technician is one who sees everything and can also quickly […]
Read more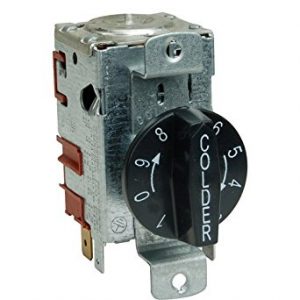
This article is written by Christopher Stephens of JVS Refrigeration in California, with just a few additions by me (Bryan) in italics. Thanks, Chris! Reach-in refrigerators are an interesting side of our industry, often looked at as frustrating and troublesome. Since we usually see reach-ins in kitchens or convenience stores, the refrigerators are never […]
Read more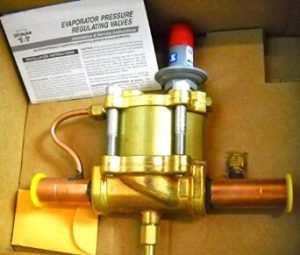
I don't do much in the way of “rack” refrigeration. However, I recently had a conversation with experienced rack refrigeration tech Jeremy Smith, and he got me thinking about EPR valves. I've heard EPR (evaporator pressure regulator) valves called suction regulators or hold back valves. In essence, they hold back against the suction line to […]
Read moreVideos:
Podcasts:
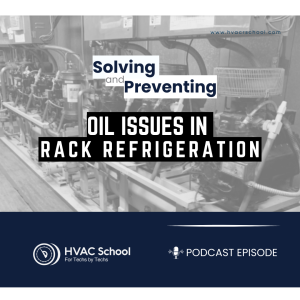
In this HVAC podcast episode, hosts Bryan Orr and Matthew Taylor (refrigeration leader and trainer at Kalos Services) discuss oil management and considerations in supermarket refrigeration systems, with a focus on solving & preventing oil issues. They talk about the importance of stable system operation and how oil flows through both active and passive […]
Read more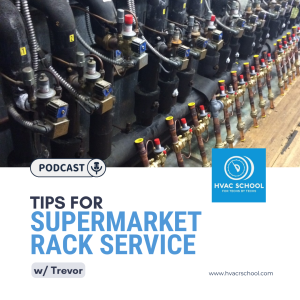
Refrigeration Mentor Trevor Matthews returns to the podcast to share some of his tips for supermarket rack service. The supermarket refrigeration world is ripe with high-paying opportunities and uses similar skills that HVAC technicians use daily. Switching from HVAC to refrigeration will require a little bit more attention to some new components, especially controls […]
Read more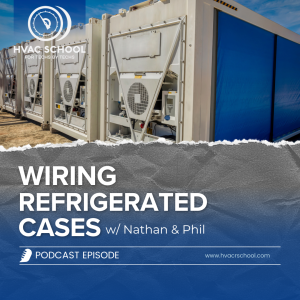
Phil Barr and Nathan Orr join the podcast to talk about wiring refrigerated cases in commercial spaces, including convenience stores and supermarkets. Cases may be medium-temp (or high-temp, in some cases) or low-temp. Medium-temp cases can typically defrost on their own during the off cycle, and low-temp cases may have electric or hot-gas defrost […]
Read more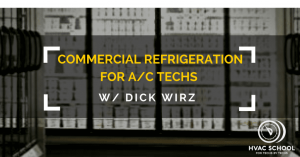
Dick Wirz, author of Commercial Refrigeration for Air Conditioning Technicians, talks about making the switch from A/C to refrigeration. Dick Wirz is an advocate for using rules of thumb, which is a controversial position. However, rules of thumb are an excellent way for A/C techs to dip their toes into the refrigeration world. Rules of […]
Read more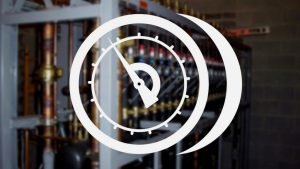
In this episode of the HVAC School Podcast, Bryan talks with Jeremy Smith about refrigeration tips, terms and processes. They also cover the similarities and differences between A/C and refrigeration. Being on-call as an A/C tech is not all that different from being on-call as a refrigeration tech. Similarly, the principles of heat transfer don't […]
Read more