BACK
Valve Core Removal Tools
Should I Pump Down or Recover?
Weighing Refrigerant In and Out
Refrigerant Recovery Practices
How much PRESSURE is that Recovery Tank Designed For?
Do You Need to Be Recovering Into a Vacuum?
Calculate Recovery Tank Fill the Easy Way
Recovery Tank Capacity
Replacing a Piston w/ TXV and Evacuation
Refrigerant Recovery Practices
Molecular Transformator – Short #217
Vacuum and Recovery in an A2L World with Jesse Stewart
Scales – The Episode You’ve been Weighting For (Podcast)
EPA Section 608 Changes Every Tech and Contractor Needs to Know (Podcast)
Evacuation, Recovery, and Dehydration Facts Podcast
Understanding Effects of A2L Refrigerants on Tools, Recovery, and Evacuation
#recovery
Tech Tips:
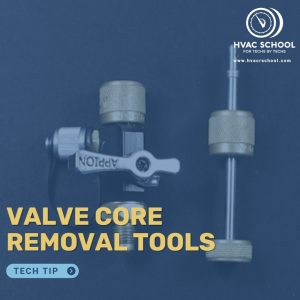
Valve core removal tools were originally developed to remove damaged valve cores without the need to pump the system down. This technology was a major leap forward in work efficiency, as pumping down a system can be a tedious and time-consuming task. Eventually, technicians discovered that removing valve cores led to faster evacuation, recovery, and […]
Read more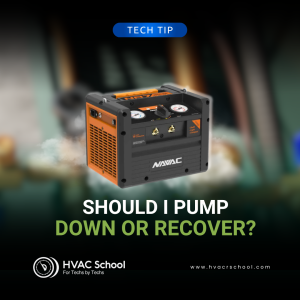
During my second year in HVAC, the company I worked for was hired to fix some poor work that was done on a multi-head inverter system. The system used flare connections, and many of them were leaking. The system also had a branch box, which meant there were even MORE flares. So we pumped all […]
Read more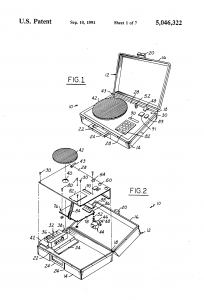
If you don't use a scale every time you add or remove refrigerant, I suggest you begin doing so immediately, if not sooner. Weighing in while charging is fairly obvious, and it's useful so you can keep track of what you are using and how much to charge a customer. When you have a system […]
Read more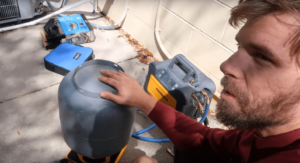
Recovery is the removal of refrigerant from a system. From there, you can either store it and send it in for recycling or reintroduce it back into the same system. Here are some top tips: Make sure your tank is empty and evacuated to 300 microns if you plan to return the refrigerant to the […]
Read more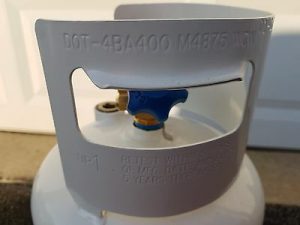
Most techs know that you shouldn't fill a recovery tank more than 80% with liquid-based refrigerant. Many know that the WC rating stands for “water capacity.” So, you need to adjust for the density of the actual refrigerant rather than just using 80% of WC. I hope most of you know that the TW marking […]
Read more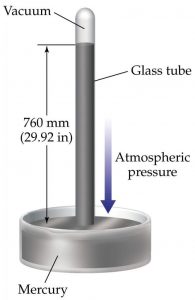
This topic came up because I was testing out the new MR45 digital recovery machine. That machine goes off by itself when it hits a 20″ Hg vacuum. It's a cool feature, but it is good to know when that level of vacuum is overkill and when it's not enough according to EPA requirements. You […]
Read more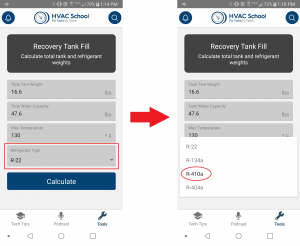
Recovering refrigerant sounds like an easy task at first, especially with digital recovery machines and large hoses at our disposal. Unfortunately, we all know that filling the tanks is more complicated than it seems. If you want to recover refrigerant and store it in a tank safely, you’re going to have to do some math. […]
Read more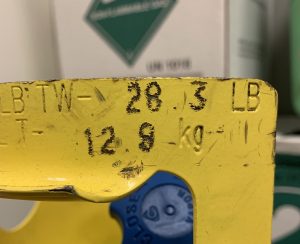
To start, I'm going to cut straight to the part that most of you want to know. This information is based on calculations I have done personally based on typical Mastercool DOT tanks, but feel free to come to your own conclusions based on your own calculations. I prefer to stay on the safe […]
Read more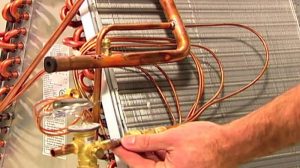
We get a lot of questions about both evacuation procedure and TXVs so last week we produced videos on both topics, including: • Before and after testing of piston vs. TXV • Using the Bluvac Measurequick app • Use of core remover tools for evacuation • Flowing nitrogen • creating an external equalizer port and […]
Read moreVideos:
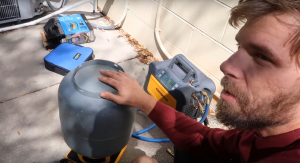
Recovery is the removal of refrigerant from a system to either store and send in for recycling or to reintroduce back into the same system. Here are some top tips – Make sure your tank is empty and evacuated to 300 microns if you plan to return the refrigerant back into the system. Never mix […]
Read morePodcasts:

In this short podcast episode, Bryan talks about the CPS Molecular Transformator and what it does. The Molecular Transformator is a version of a tube-in-shell heat exchanger, which is a method of exchanging heat from one fluid medium to another fluid medium. Tubes containing a fluid pass through a shell containing water or glycol, […]
Read more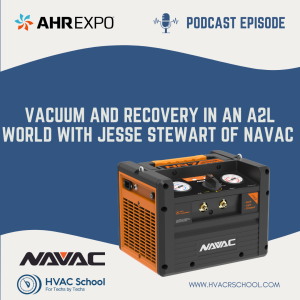
In this podcast, Bryan Orr interviews Jesse Stewart from NAVAC about A2L refrigerants and compatible tools and safety procedures. They discuss how NAVAC has a full line of A2L-compatible tools for evacuation and recovery, including the new NR7 and upgraded models of the NRDDF and NRDD. Jesse explains key features that make tools A2L […]
Read more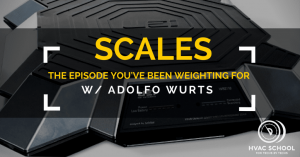
Adolfo Wurts from Arbiter Incorporated, designer of the UEI WRS line of Bluetooth scales, comes on the podcast. We talk all about scales and how to use them. You'll want to pull a scale off your truck every time you add refrigerant to a system. Many technicians choose to estimate how much refrigerant they have […]
Read more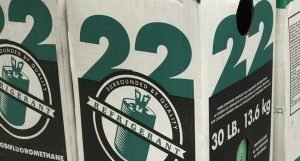
In this episode of the podcast, Jeremy Arling from the EPA comes on and answers some common questions about the new rule changes that affect recovery, leak repair, recordkeeping, and evacuation on HVAC and refrigeration systems. EPA 608 rules regulate the actions that technicians must take when it comes to refrigerants and the atmosphere, such […]
Read more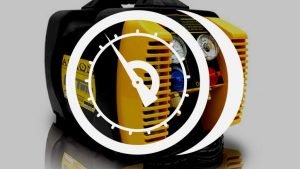
In this episode, Bryan covers evacuation, recovery, and dehydration. Evacuation refers to putting a vacuum pump on the system and pulling it down. We use a few different measures of vacuum, including inches of mercury (“Hg) or microns (millionths of a meter of mercury). We use such small units to measure a vacuum that effectively […]
Read moreEvents:
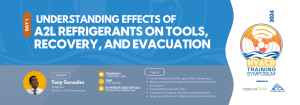
NOTE: If you cannot view the recording, the video may still be processing. The maximum wait time is 24 hours. We apologize for the delay and appreciate your patience.
Read more