BACK
Switch Terms
Discovering Mental Reference Points
Short Circuits
Understand Heat Pumps
Isolation Diagnosis
Michael Faraday: Patron Saint of HVAC Technicians
Blower Fan Watt Draw Considerations for ECMs
Tool Selection: Electrical Meters
Understanding 240-Volt Circuits
Don’t Overfill Refrigerant Recovery Cylinders The Easy Way
Something You May Want to Consider on Every Call
Motor Tap Battle
When 0V Isn’t Safe – Short #242
Multiple Surge Protectors – Short #236
MCA is 27 and the Breaker is a 50A – Short #219
Deploying Surge Protection & Voltage Monitoring w/ DITEK
Surge Protection Basics w/ DITEK
What Is Up With Blower Amps & Watts w/ Steve Rogers
Residential & Rack Startup and Commissioning (Part 1)
History of AWG – Short #186
Analog vs. Digital Sine – Short #179
#electrical
Tech Tips:
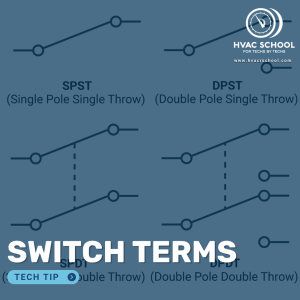
A while back, I had a tech who was having some trouble finding a 35 PSI (2.41 bar) make-on-fall pressure switch. One adjustable switch in the catalog said (SPDT), but he didn't quite understand what that meant. In that case, it means single-pole, double-throw, and the “double-throw” part means that the switch has terminals in both the […]
Read more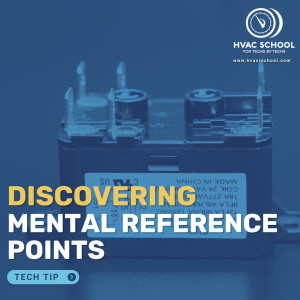
Trying to wrap your head around HVAC can feel like a constant firehose of new info, right? Whether you're in class or on the job, there's just so much to soak up. And when you finally think you've got one thing down, BAM, here comes another concept. For me, remembering everything can be a real […]
Read more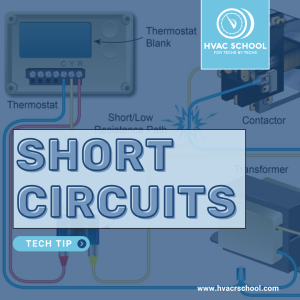
The term “short” has become a meaningless phrase in common culture to mean “anything wrong with an electrical device.” In reality, a short circuit is a particular fault that can mean one of two things in technical lingo: 1. Any two circuits that are connecting in an undesigned manner. This issue would be the case […]
Read more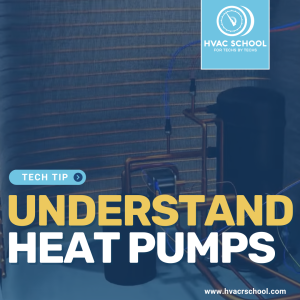
My goal in this tech tip is to help those who struggle to understand heat pumps get their heads around them as quickly as possible and understand some of the things a tech needs to know about them. The basic idea of a heat pump is to use the compression refrigeration cycle to move heat […]
Read more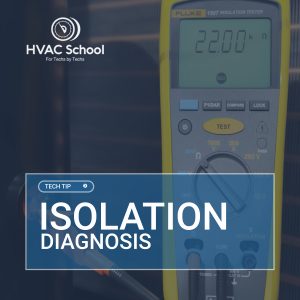
There are many great diagnostic tools available to the service technician today, but I haven't found a tool as versatile as the simple isolation diagnosis. There are many ways this concept can be applied, but let's start with some examples so that you get what I mean. Low Voltage Short Circuit Isolation Diagnosis You arrive […]
Read more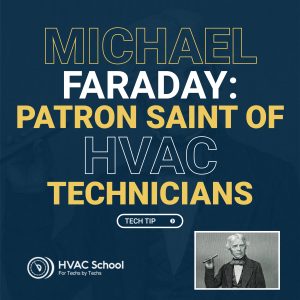
Who was Michael Faraday—besides the guy we named the capacitor after? Well, actually, we named the measure of capacitance after him (the farad), but let’s not get all caught up in semantics. Faraday was a scientist who lived from 1791 to 1867. He was an experimental scientist who had little to no formal education but […]
Read more
I'd like to give special thanks to Steve Rogers from TEC for helping write this tech tip and sharing some helpful visuals. Thanks, Steve! ACCA Standard 310 introduced a grading protocol for HVAC systems. While HVAC practitioners won’t be the ones carrying out the tasks laid out in Standard 310, energy raters will conduct them […]
Read more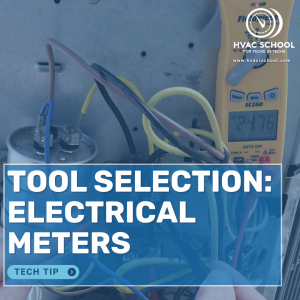
I'd like to give a special thanks to Tony Gonzalez from Fieldpiece for providing technical guidance about the SC680's power measurement capabilities, as well as VAC and AAC measurements on ECMs. We’ve talked through specifications, applications, and features for a few tools, but none of them have been quite as hardcore as electrical meters. Like […]
Read more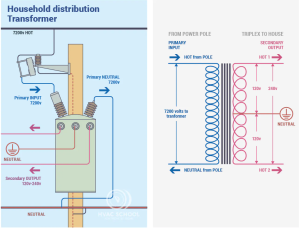
It can be useful to think of a multimeter as a “voltage drop” tool. Bryan covers the concept here in an excellent class that I highly recommend. This concept was a big help to me as I began to truly learn how to use a multimeter. A meter reads the voltage differential between two points. […]
Read moreVideos:
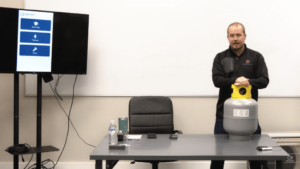
In this video we review the HVAC School app tank fill calculator and how to use it to prevent the overfilling of refrigerant recovery cylinders.
Read more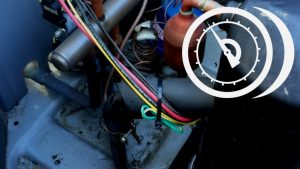
There are a few important things that I suggest checking on every service call to reduce callbacks and increase customer satisfaction. One of them that often gets missed is preventing wire rub outs. One of my area managers and experienced tech Jesse Claerbout shot a video showing the simple step he takes to prevent major […]
Read more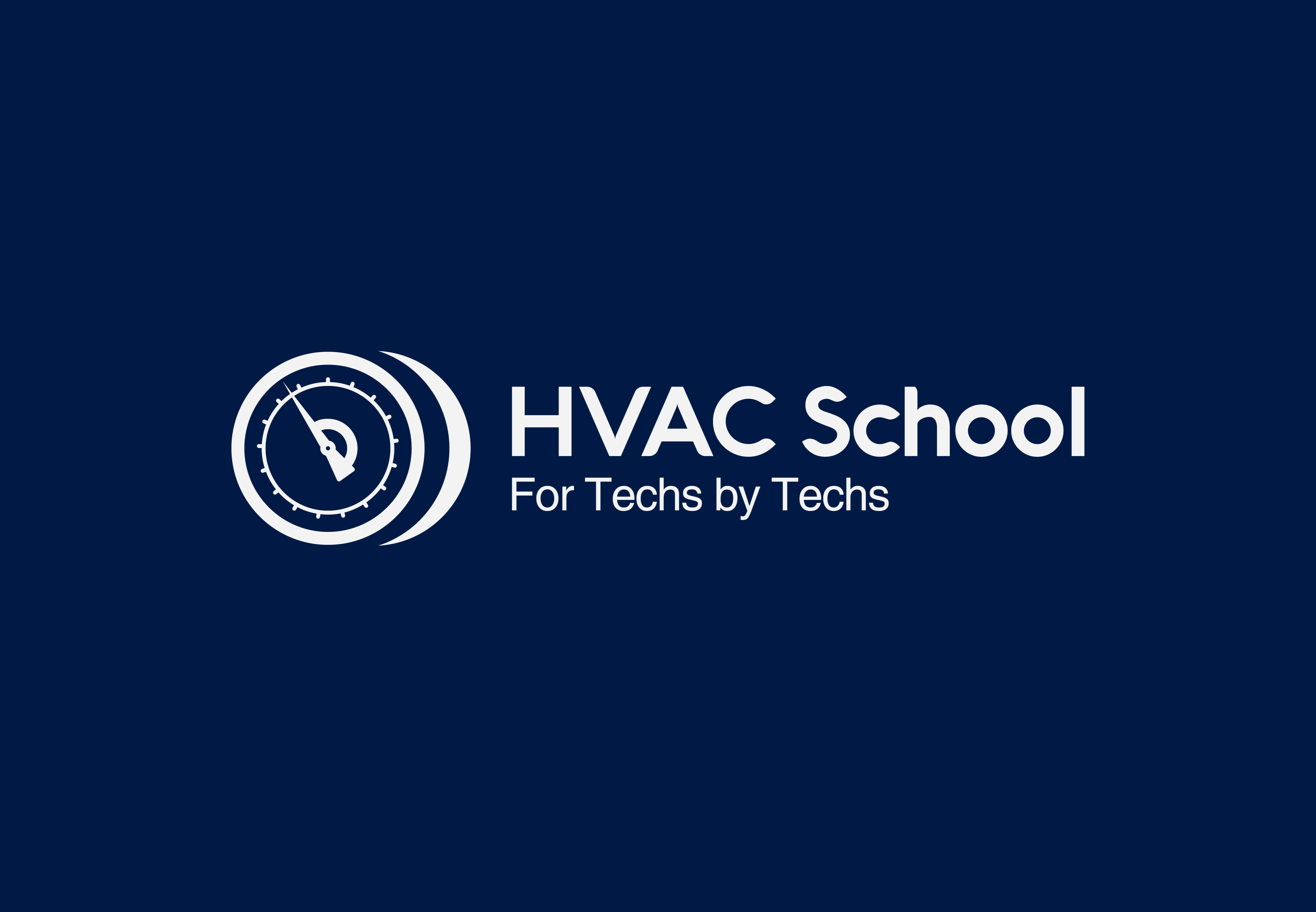
In this video we cover Basic Motor Wiring Run, Common and Start legs Multi Speed motors and whether the speed taps are common, run or start The location of a thermal overload in a multi speed blower motor If you have an iPhone, subscribe to the podcast HERE, and if you have an Android phone, […]
Read morePodcasts:
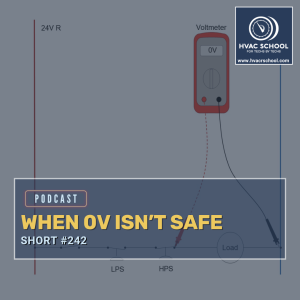
In this short podcast episode, Bryan covers some unique electrical cases: when 0v isn't safe. When you measure voltage, you're finding out the electrical potential between two points. Just because there is 0v between one point and another doesn't mean there will be 0v between those points and other points. Non-contact voltage detectors are […]
Read more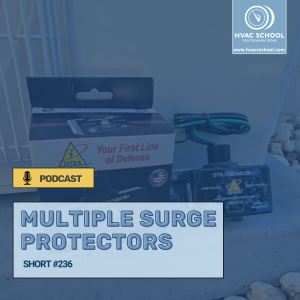
In this short podcast episode, Bryan answers a listener-submitted question asking whether you can use another surge protector at the disconnect panel with an ICM 493 already in place. Using multiple surge protectors in the configuration described does NOT count as daisy-chaining. Surge protectors with MOVs (metal oxide varistors) shunt current from high voltage […]
Read more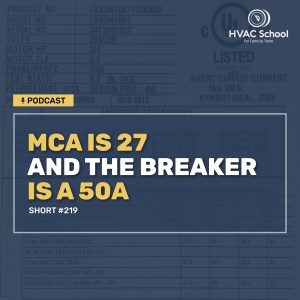
In this short podcast episode, Bryan and Mike from DITEK talk about what to do in tricky electrical scenarios, such as when the MCA is 27 and you have a 50A breaker. When you size an HVAC system for compatibility with voltage monitors, like the DITEK Kool Guard, you need to pay attention to […]
Read more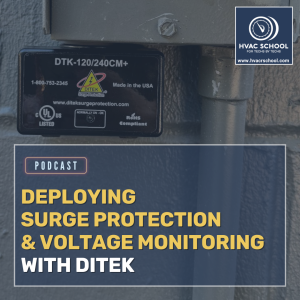
Bryan discusses surge protection devices (SPDs) with Mike from DITEK, focusing on practical applications for HVAC contractors and how to provide value to clients. Mike emphasizes that surge protection is essential for modern HVAC systems, particularly given that they are typically the most expensive appliance in a home and increasingly rely on sophisticated electronic […]
Read more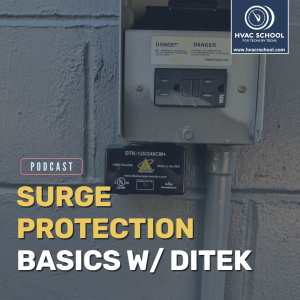
In this enlightening episode, we sit down with Mike, a 20-year veteran from DITEK, a leading American manufacturer of surge protection devices based in Largo, Florida. The conversation begins with a brief discussion about recent hurricane impacts in the Tampa Bay area, where DITEK maintains its 65,000-square-foot manufacturing facility. Mike shares how the company, […]
Read more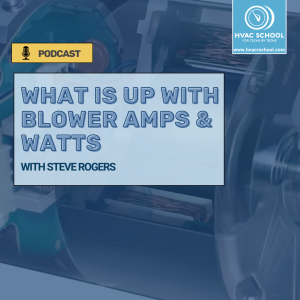
Bryan Orr and Steve Rogers dive deep into measuring power consumption in HVAC blower motors, particularly focusing on the differences between PSC (Permanent Split Capacitor) and ECM (Electronically Commutated Motor) technologies. The discussion stems from a question raised at an educators' conference about the accuracy of clamp-on meters in measuring blower motor watt draw, […]
Read more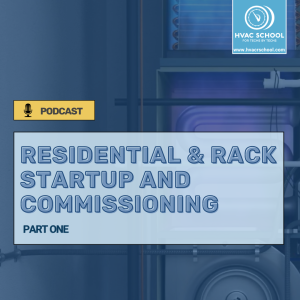
In this episode of the HVAC podcast, Bryan and Max Johnson from Kalos discuss the critical role of a startup and commissioning technician in the HVAC industry. Max, who has experience in both residential and commercial HVAC, shares his insights on the importance of understanding the scope of work, equipment specifications, and code requirements. […]
Read more
In this short podcast, Bryan explains the history of AWG, or American wire gauge, which is the sizing system we use for conductors in the United States. Wires weren't standardized before the 18th century (1700s). As fencing, telegraph, and electrical wires started coming out, there was a need for a standardized system. In England, […]
Read more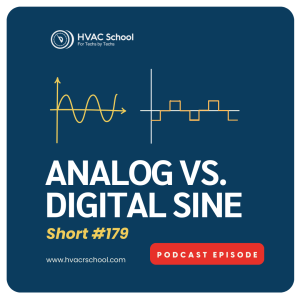
In this short podcast, Bryan breaks down the differences between analog and digital sine waves. Analog readings deal with an unlimited number of values; they are very precise and can have any number of decimals. As a result, the alternating current (AC) analog sine readings have very smooth curves when we read them on […]
Read more